An ultrasonic flaw detector is the equipment that is designed to detect defects in an object without damaging its integrity. Deformations are detected through the impact of ultrasonic waves on the object. The equipment is in great demand, because the method of its operation is the only one that allows you to provide the most accurate diagnostic results without disassembling the object of research.
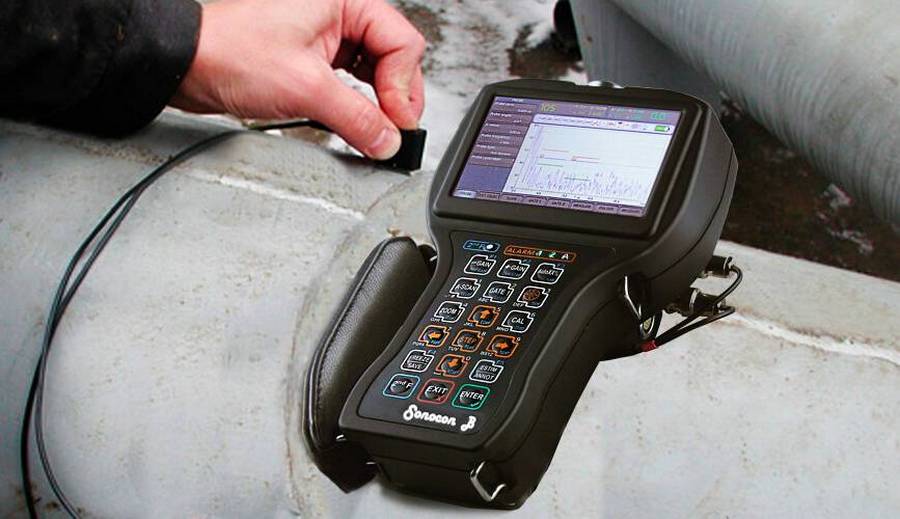
Ultrasonic flaw detector: general information
Ultrasound passes through a layer of solid iron and is able to detect the presence of the smallest cracks that may be inside the object. The device will be able to detect a defect at a depth of 5 to 50 millimeters with high accuracy. The equipment under consideration may have different levels of sensitivity. This indicator depends on the size and dimensions of the detected defect. The scope of the device is very wide, but most often they are used to determine the quality of metals in production.The devices have intuitive operation, provide a unified and efficient use, and are characterized by increased accuracy, which allows you to obtain high-quality results and timely detect and correct various production flaws.
Principle of ultrasonic control
The type of apparatus under consideration is usually used to control the level of strength at welds. In this case, the device operates as follows during operation: specific acoustic waves are directed into the metal sheets, causing vibrations in the case. They can be of the following types:
- Hypersonic;
- ultrasonic;
- Standard sound;
- Infrasonic.
During the passage of ultrasound, the space through which it propagates forms uniform oscillations with respect to its rest point. For solids, transverse/longitudinal vibrations can occur, which allows you to control the quality of welds with maximum accuracy. The speed of propagation and supply of the described waves is directly dependent on the strength / internal environment of the object under study. The intensity of the waves can be adjusted. As the wave propagates, its strength will gradually fade away. Based on the control of the rate of this extinction, it will be possible to judge the strength of the seam. The device, on the other hand, will display the attenuation coefficient of ultrasound, creating it based on the degree of absorption and scattering. The final accuracy is very high, so you can get specific ideas about the quality of the metal, the strength of the seam and the absence / presence of other defects.
Popular types of modern production flaw detection
Extremely popular non-destructive flaw detection instruments include: eddy current, acoustic (ultrasound) and magnetic. There are other types, but their use is not so widespread, because the principle of their work is somewhat complicated.
Ultrasound (acoustic format)
An acoustic flaw detector is commonly understood as a set of non-destructive testing devices similar in their functionality. Their action is based on the principles of acoustic waves. According to the simplest physical principles, the basic indicators of a sound wave cannot be changed when propagating in a homogeneous microenvironment. However, if a new medium blocks the path of the wave, then its length and frequency change. The higher the sound frequency, the more accurate the result will be, therefore, among the entire available range, ultrasound is used. The ultrasonic device emits waves that penetrate the test object. If there are cavities or inclusions of other materials, as well as other defects, then the wave will invariably detect them, showing this by changing its parameters.
Flaw detectors operating on the principle of echolocation are considered the most accessible and widespread. The wave enters the object and, if no defects are found, it is not reflected, respectively, the device does not receive a feedback and no violations are registered. If the wave returned back, then this indicates the presence of flaws. In any case, the device itself is both a generator and an ultrasound receiver, which greatly facilitates flaw detection operations. The mirror mode of action is a bit like echolocation, but it uses separate devices - this is a generator and a receiver.The advantage of this method is that both devices are located on the same side of the object under study, which qualitatively simplifies the procedure for setting up, adjusting and taking measurements. Separately, it is worth mentioning the methods of ultrasonic analysis. The concept of "sound shadow" is used here. If there is a defect inside the object, then it will contribute to the instantaneous damping of vibrations, thereby creating a “shadow”. This principle is based on the shadow method of flaw detection by means of ultrasound, in which the receiver and transmitter are on the same sound axis, but on opposite sides. The disadvantages of such a device are that for its full-fledged operation, strict conditions must be met for the dimensions, configuration, and roughness level of the object being measured, which indicates poor unification of the equipment.
Eddy currents and magnetic fields (eddy current format)
Vortex flows are created in conductors when forming in the immediate vicinity of an alternating type magnetic field, based on the fact that in the presence of defects, these flows reproduce their own secondary field, and eddy current flaw detection devices operate. As a result, the described apparatus of such a principle of operation forms a primary field, and a secondary field, which provides an opportunity to detect and identify shortcomings in the subject of research, is created as a result of electromagnetic induction. The device, on the other hand, receives a secondary field, registers its indicators and gives a result about the type and quality of the defect.
Such devices have very high performance, and the verification process does not take much time.Nevertheless, vortex flows occur only in those media that have a conductive ability, which indicates the narrow specialization of this apparatus.
Magnetic particle format
This is another of the most common ways. It is used in evaluating welds, checking the strength of protective layers, the reliability of pipe lines, etc. This method is especially valuable for diagnosing objects with a complex geometric shape and places that are difficult to access for verification.
The operating principle of this method is based on the physical parameters of magnetized metals. By means of permanent magnets (or their analogues) capable of forming a circular/longitudinal magnetic field, a special reagent, a magnetic powder, is applied to the test object (wet/dry method). Under the influence of the field, the powder will be combined into so-called chains, structured and form a distinct pattern in the form of wavy lines on the surface. The resulting image will clearly demonstrate the operation of the field, and knowing the necessary parameters of the curved lines, you can see where there are discrepancies and determine the location of the defect. Usually, a particularly large amount of powder accumulates at the location of the defect (cavities, cracks). The final result is fixed by comparing the resulting image with a quality standard.
Other types of flaw detection
New techniques appear constantly, almost every year. At the same time, the old ones immediately lose their former popularity. Many modern devices are highly specialized and are used only for specific industries.
For example, fluxgate devices operate by analyzing the impulses that are created when it moves along the object.They are used in the production of rolled metal products, in general metallurgy and in the inspection of welds.
Radiation devices in operation irradiate objects with alpha, beta, gamma and X-rays, as well as bombard them with neutrons. The result is a very detailed image of the object with visible inhomogeneities and defects. The method is characterized by high cost, which is compensated by increased information content.
Capillary models are designed to detect external cracks and gaps when exposed to a special developing agent. The result is evaluated purely visually. The capillary method is used in shipbuilding, aviation and mechanical engineering.
In the energy industry, all imperfections in products (which are under high voltage) are detected by electron-optical flaw detectors. They can capture the smallest changes in surface-particle and corona discharges, which makes it possible to analyze the operation of an object remotely, without stopping its operation.
Preparing for diagnostics
Prior to the start of the test, it is necessary to clean the surface from traces of corrosion, paintwork materials and other coatings. However, it is not necessary to clean the entire surface, it is enough to observe a gap of 70 centimeters. In this form, the object will be prepared for diagnostics, but it would still be preferable to additionally check the patency of the ultrasonic wave. To do this, you can use oil, grease, glycerin, and other liquid substances with a fat content. Next, you will need to adjust and calibrate the scanning device for specific options. The main tasks are:
- Checking objects with a thickness of less than 20 millimeters (it is allowed to use the factory default settings);
- Examination of objects with a thickness of more than 20 millimeters (the data of the ART diagram is added to the settings);
- Diagnosis of the reliability of welds (complex calibration with ART-diagram data and clarification of other complex impulses will be required).
Only after the configuration is completed, you should proceed with the verification operations.
Achieving the highest level of research accuracy
In order to obtain maximum accuracy of the result, the probe of the device must be moved in a zigzag manner over the surface, while it is necessary to rotate the probe around the axis by about 10-15%. If the device starts to produce atypical vibrations, then in the detected place it is necessary to expand the probe as much as possible in order to more accurately determine the location of the poorly made connection. The search is required to be carried out until the point at which the peak of the wave will be the highest is known. At the same time, it must be taken into account that the equipment can return the result with some error, which is a consequence of wave reflection from the seams. Then other diagnostic methods should be applied. If several different methods lead to a single result, then you can fix the flaw by writing down its coordinates. Manufacturers of flaw detectors rely on the requirements of the State Standards and recommend testing one object with at least two different methods. All data obtained must be recorded in a special journal or table. So you can quickly eliminate the defect in the object and speed up the final diagnosis, because all identified problem points are already known.
Defects that are detected by ultrasonic flaw detectors with the highest probability
The control of welding seams, carried out by means of devices of the type in question, allows you to get a clear picture of the situation.Properly performed procedure can guarantee almost 100% accuracy of the result. However, there are drawbacks that are quite difficult to detect. But there are a lot of detected 100% defects, and they include:
- Chips, cracks;
- Pores;
- Welds undercooked;
- Lamination of metal alloys;
- fistulas;
- Sagging seams at the beginning / end of the entire structure;
- Traces of corrosion;
- Mutual exclusion in one joint of two different metals;
- Deviation from geometric indicators in the design scheme.
The research carried out on such types of metals as:
- Steel,
- Copper,
- Cast iron.
Also, the following types of sutures are available for diagnosing ultrasound:
- T-shaped;
- flat;
- transverse;
- Longitudinal;
- Ring.
Advantages of ultrasonic flaw detectors
They may include:
- Increased accuracy and accelerated collection of evaluation information;
- The low cost of the procedure itself;
- Portability of the equipment used, which allows work "in the field";
- The possibility of conducting research without interrupting the operation of the diagnosed object;
- No risk to welds, pipe cavities and other solid substrates.
Difficulties of choice
The main parameters that require close attention before the purchase can be called:
- Measurement range;
- Purpose and purpose;
- Overall performance;
- Complexity of assembly/configuration;
- Limits of operating temperatures;
- Reliability.
Different models have different measuring ranges, which means that some instruments can detect defects down to one micrometer, while others are limited to ten millimeters. Such detail plays a very important role, for example, in mechanical engineering, but for construction purposes, high accuracy is unnecessary.Thus, for the latter industry, there is no point in acquiring an accurate and expensive instrument. Also, in the accompanying documents, the manufacturer must indicate for what type of materials a particular model is intended, as well as what shortcomings it can reveal. Separately, special requirements may be imposed on the nature of the surface, the presence / absence of protective layers, the shape and dimensions of the test item.
The performance indicator determines the speed of scanning and the object of the procedure, which can be "attached" to a specific time unit. So, fluxgate and eddy current models can provide increased speed, but the process of magnetization and work with each section separately can take quite a long time. Separately, it is worth mentioning the installation / assembly / configuration process. Hand-held portable devices that fit easily into a bag will be the best solution for duty inspection service. More precise and complex devices will always require additional installation/adjustment time. In view of the fact that non-destructive testing can be carried out both indoors and outdoors (including the cold season), it is necessary to determine the limits of operating temperatures. At the same time, you need to take care of the possibility of working in aggressive environments.
Rating of the best ultrasonic flaw detectors for 2025
Budget segment
3rd place: "TUD-1 Sonel Ultrasonic Leak and Electrical Discharge Detector"
The model can accurately determine the place of depressurization (the place of leakage of gases/liquids, the place of loss of vacuum).It is used for: control of oxygen supply, automatic fire extinguishing systems, during installation of air conditioning and ventilation, examination of insulators in contact networks, diagnostics of objects of development, storage and processing of petroleum products / gas products, search for points of damage to brake systems at cars, detection of electrical discharges in low-voltage ASUs at distance up to 10 meters, and in high-voltage - at a distance of up to 30 meters. It works on the principle of registering the occurrence of defects in materials, which is accompanied by a sharp change in acoustic radiation, including in the ultrasonic region. The device converts the radiation into signals in sound / graphic forms, and the operator fixes the defects and makes a decision on the need for repair work. The model works without contact, and it does not need to disconnect the subject from the power supply or stop the equipment. The device has a manual adjustment of the signal strength, which allows the device to be adjusted to the individual characteristics of the operator. Application is also possible at negative temperatures down to -20 °C. The recommended cost for retail chains is 32,760 rubles
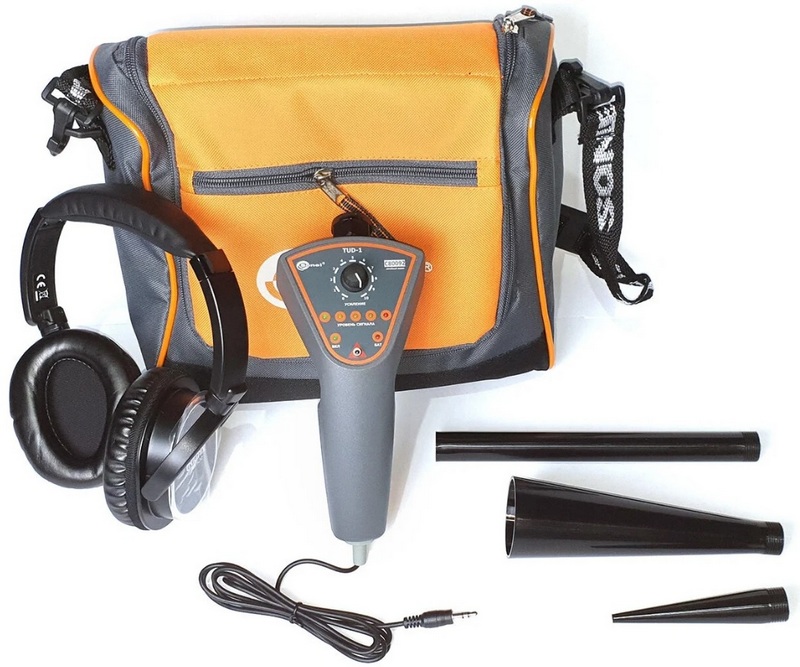
flaw detector TUD-1 Ultrasonic leak and electric discharge detector Sonel
Advantages:
- Practical versatility;
- Sufficient operating temperatures;
- Adequate price.
Flaws:
2nd place: "Inatest hardness tester combined: ultrasonic and dynamic (ultrasonic Inatest-U with probe type "A" with verification)"
This model is considered universal, because it is possible to order a lot of additional equipment for it, expanding its functionality. For example, it can work with 7 different types of sensors for cast iron, steel gears and slots, thin metal products, etc.Work in specific conditions of control of hardness is possible. Three variants of sensors for measuring galvanic vibrations are supplied as standard. The recommended cost for retail chains is 71,880 rubles.
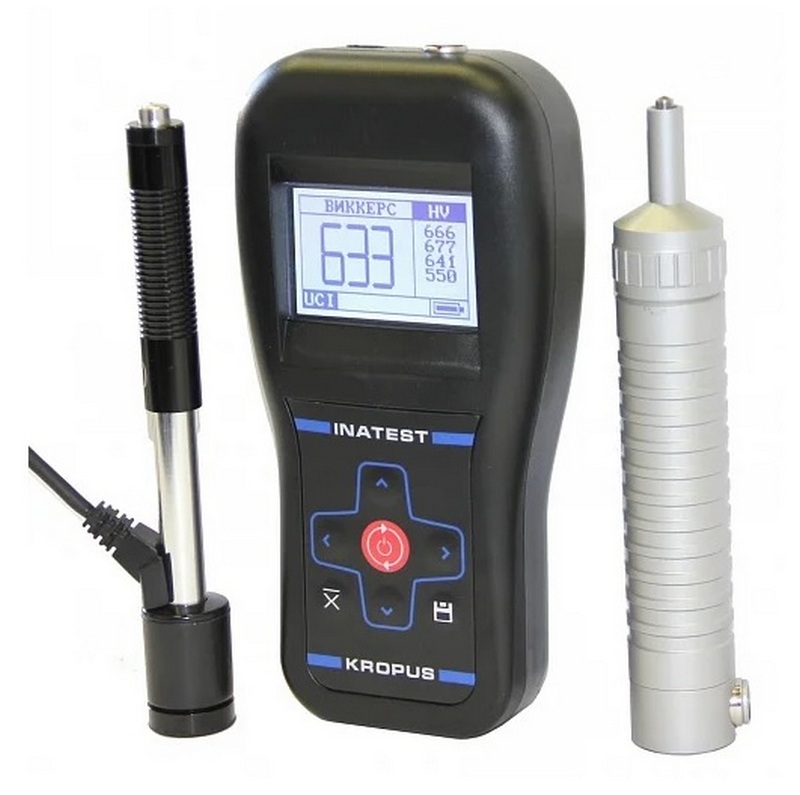
flaw detector Inatest combined hardness tester: ultrasonic and dynamic (ultrasonic Inatest-U with sensor type “A” with verification)
Advantages:
- Possibility of optional addition of sensors;
- Versatility;
- Work in special conditions.
Flaws:
- The need to purchase additional components for a specific task.
1st place: "TVM-UD hardness tester combined: ultrasonic and dynamic (ultrasonic TVM-UD with verification)"
Another prefabricated model, the quality of which is confirmed by its inclusion in the official register of measuring instruments used by the state company Russian Railways. The modification is considered universal, but as standard it has only one type of sensor (US). It is possible to connect up to 10 other types of sensors, up to dynamic and galvanic. The recommended cost for retail chains is 85,511 rubles.
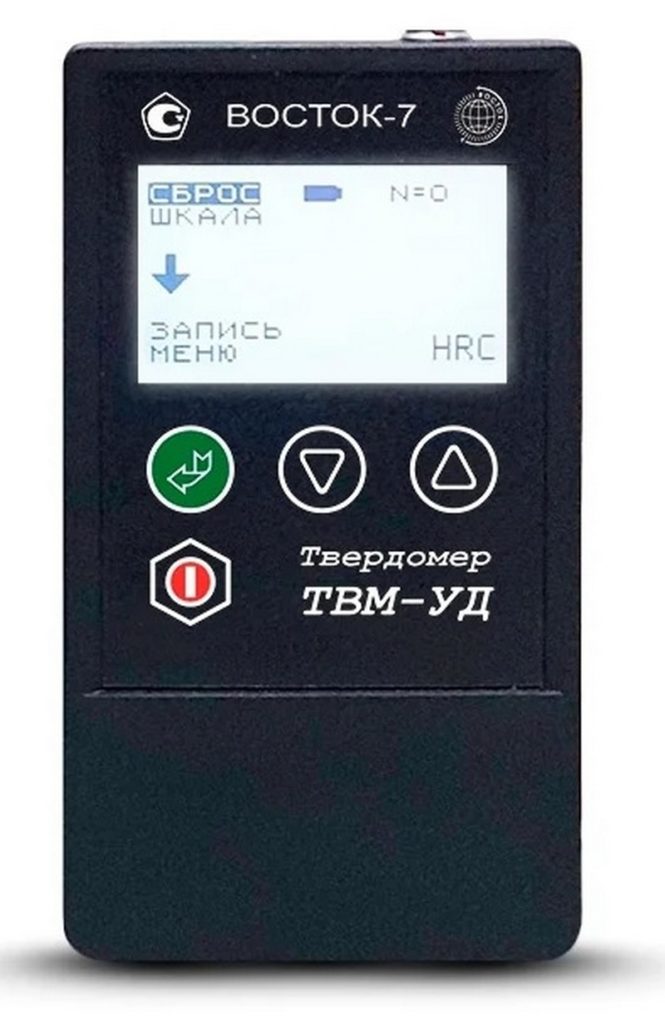
flaw detector TVM-UD combined hardness tester: ultrasonic and dynamic (ultrasonic TVM-UD with verification)
Advantages:
- Ability to work with 10 different sensors;
- Has recognition at the state level;
- Combined mode of operation.
Flaws:
Middle price segment
3rd place: "UKS-MG4S to control the strength of building materials and rocks (UKS-MG4 with verification)"
This advanced model in its basic configuration uses only the surface wave pumping method to determine the strength of concrete and reinforced concrete products, bricks and silicate stones.It has a monoblock design, which is an electronic unit with converters in a single housing. Characterized by a high level of accuracy. The recommended cost for retail chains is 92,000 rubles.
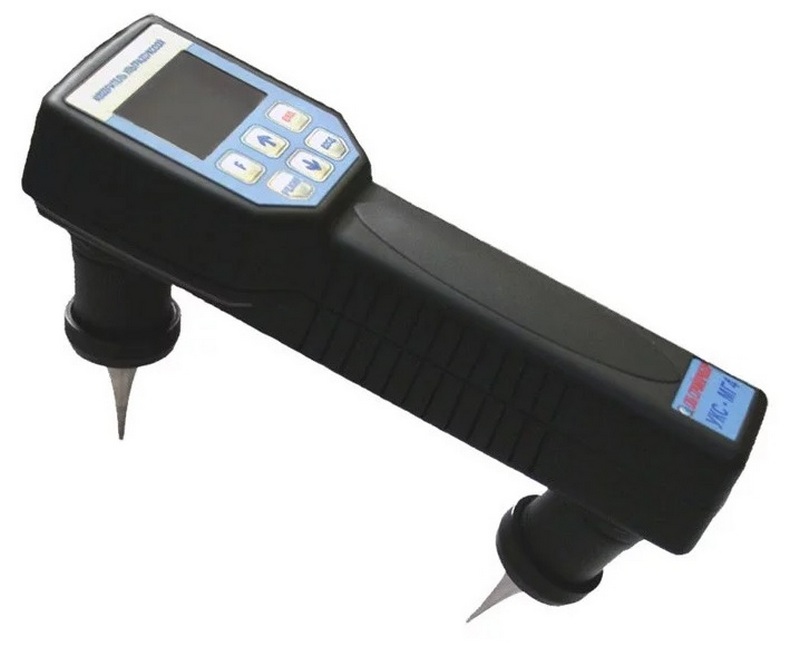
flaw detector UKS-MG4S for testing the strength of building materials and rocks (UKS-MG4 with verification)
Advantages:
- Narrow specialization (construction);
- Execution in the form of a monoblock;
- Sufficient level of accuracy.
Flaws:
2nd place: "PULSAR-2M TFT (verified)"
The excellent device which is characterized by high accuracy of the carried-out analysis. It has a design in the form of a monoblock and is perfect for non-destructive testing departments on duty. It is convenient to carry it even in your pocket, because it has small dimensions. The display is color and all controls are intuitive. There is a block of memory for storing a large amount of results. The recommended cost for retail chains is 138,000 rubles.
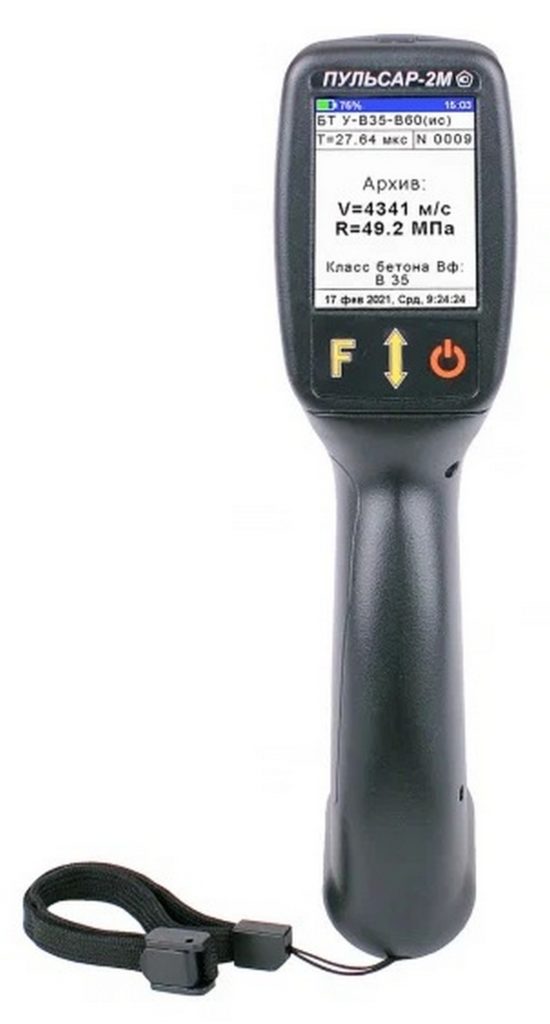
flaw detector PULSAR-2M TFT (with verification)
Advantages:
- High functionality corresponds to the declared price tag;
- Maximum portability;
- Color display.
Flaws:
1st place: "PULSAR-2.1 (verified)"
Very expensive and multifunctional sample. It can be used in a variety of applications, from construction, where medium-precision results are required, to high-precision engineering, where analyzes down to micrometers are needed. The kit comes with all possible types of sensors. The recommended cost for retail chains is 140,000 rubles.
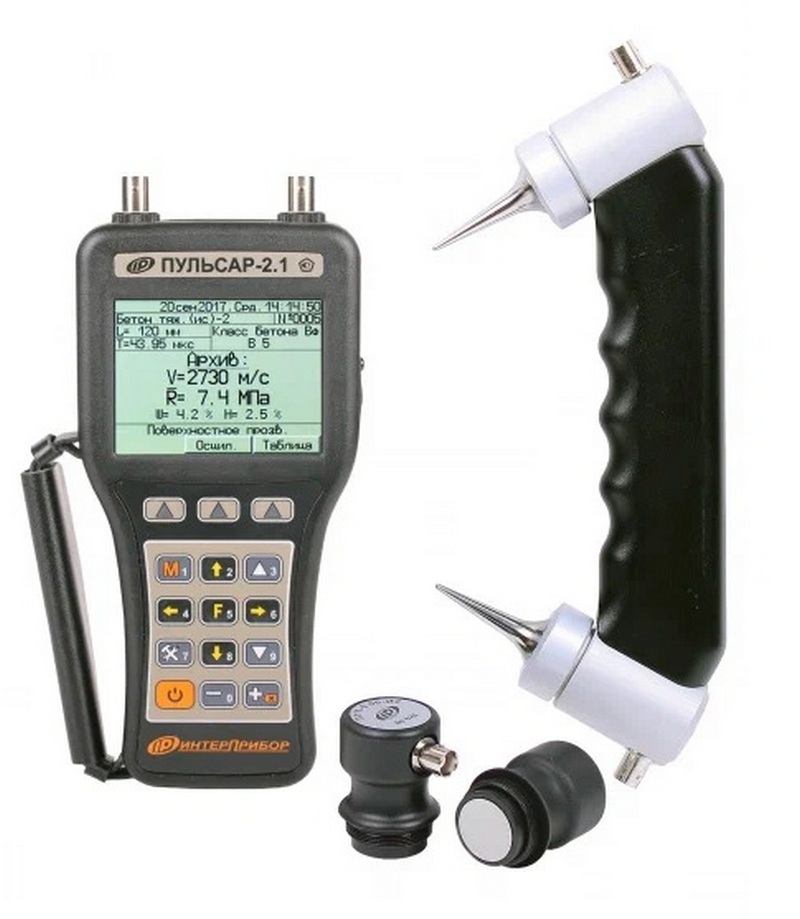
flaw detector PULSAR-2.1 (with verification)
Advantages:
- Adequate ratio of equipment and price tag;
- Wide scope of use;
- Improved accuracy.
Flaws:
Premium class
2nd place: "Submersible emitter SG-18 28kHz 900W with generator"
This device is designed to diagnose pipe lines with any diameter, is a high-precision stationary equipment and is used to control the quality of rolled metal in workshops. Especially well, its probes cope with pipes of irregular geometry and with decreasing / increasing diameter along the entire length of the line. The kit includes: platform, generator, high-frequency probe, storage case. The recommended cost for retail chains is 170,000 rubles.
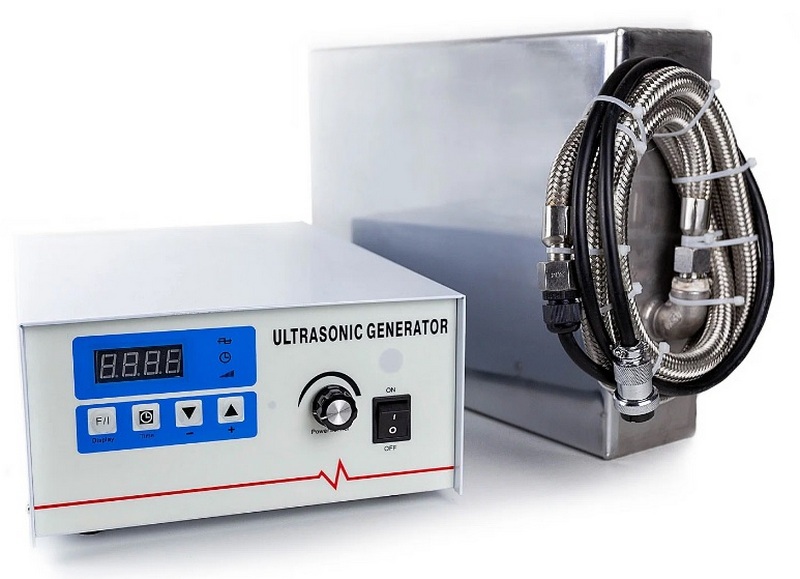
flaw detector Submersible emitter SG-18 28kHz 900W with generator
Advantages:
- Increased accuracy;
- Stationary placement;
- Ability to work with non-standard objects;
- One year warranty.
Flaws:
- Limited (industrial only) scope.
1st place: "Ultrasonic device PULSAR-2.2 (with verification)"
The latest and most modern modification of the popular Russian brand of equipment. The final release software is installed on it, it is now possible to display test graphs in dynamics. The kit includes all the most common sensors, the equipment has small dimensions. The recommended cost for retail chains is 222,000 rubles.
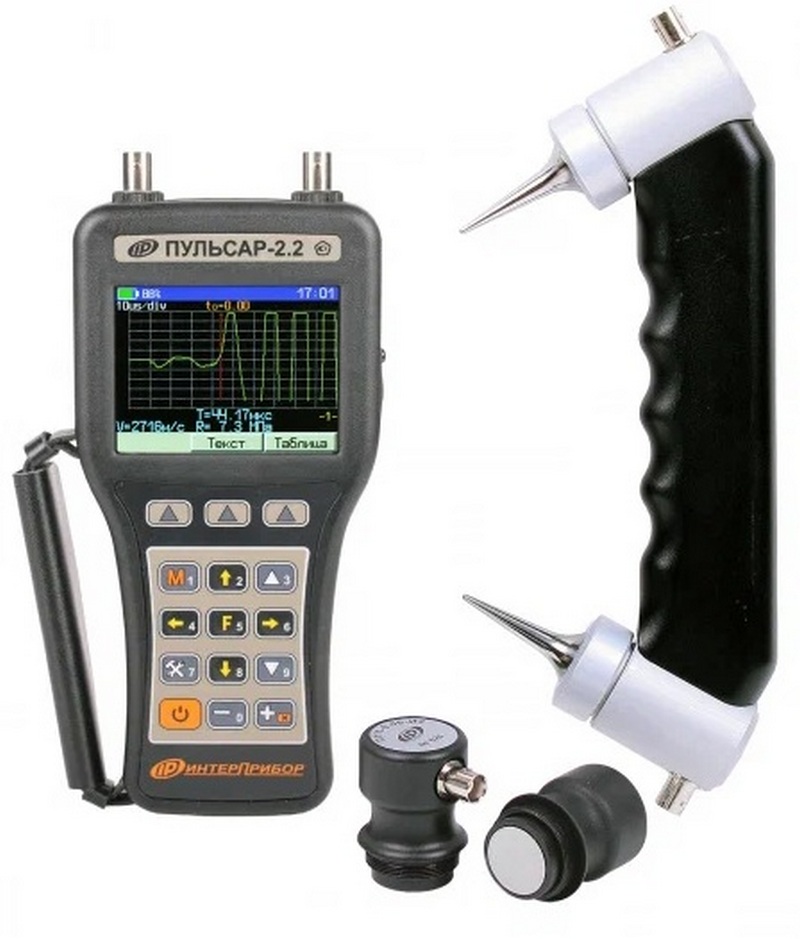
flaw detector Ultrasonic device PULSAR-2.2 (with verification)
Advantages:
- Latest software version;
- Good equipment;
- Small sizes.
Flaws:
Conclusion
It is always worth remembering that the high-precision equipment in question in terms of weight, dimensions, type of power supply, methods for detecting defects, resistance to vibrations must comply with the requirements of State Standard No. 23049 of 1984.In addition, any model must have a specific minimum of working units with which you can perform the most standard operations.