In any hammer drill there is an impact mechanism, a gearbox, as well as many elements rubbing against each other during operation, which leads to their rapid wear. Therefore, in order to prevent premature failure of the tool, it is always necessary to use a special lubricant for all these parts, which is filled with the gear housing.
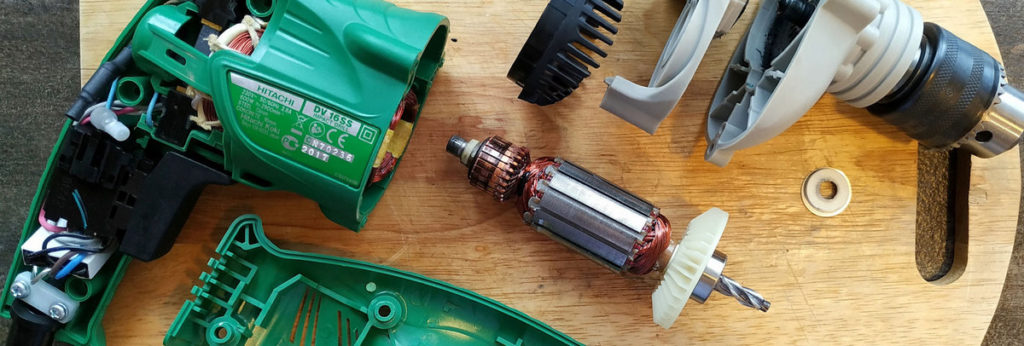
Lubricants for perforators - general information
The lubricant in question can be produced by various brands, but its main task is to ensure the easiest possible interaction between the working parts of the perforator mechanisms. First of all, it is designed to reliably envelop the protected parts, preventing their excessive friction between themselves. From this it is clear that both productivity and efficiency will be increased in proportion to the quality of the lubricant and its sufficient quantity.
The optional functions of this substance include:
- Additives, which are completed in most cases with a lubricating composition, are able to perfectly resist the manifestations of corrosion;
- Washing function - during the operation of the puncher, as a rule, a lot of dust is formed, and its smallest fragments penetrate the mechanism and can cause a breakdown or simply interfere with normal operation. By means of a lubricant, dust cannot be spread to most of the working elements, while maintaining the proper operational condition of the latter. When the lubricant retains a sufficient amount of dust, it will have to be changed.
Perforating oils can be synthetic, semi-synthetic or mineral based. The most popular are mineral types, which are produced on the basis of pure oil.However, they quickly lose their useful properties during operation, which requires their frequent replacement.
Causes of perforator overheating
In cases where, during use, the perforator began to heat up above the nominal temperature, this fact does not mean that there are questions about the oil. In most cases, this situation arises due to the intensive use of the chiseling mode, and that is why the lubricating substance simply does not reach all the mechanisms of the device in the right amount on time.
Also, the cause of overheating can be clogged holes designed to cool the electric motor. The solution for this situation is very simple: you just need to clean the device from dust, then transfer it to a different operating mode for a while. As an example: when a perforating device is used as a conventional drill, even for half an hour, the temperature of all its elements will drop significantly.
IMPORTANT! It is always worth remembering that the reducer must have a constant temperature, regardless of the mode of operation of the device.
The need for lubrication of the perforator
Modern perforating devices are divided into special classes, depending on which they can perform operations for chiselling, drilling, drilling various materials, including very hard ones, such as concrete. All these operations, during their execution, in addition to increased noise, are accompanied along the way by the release of a large amount of dust, coupled with small stone fragments.
Such extreme operating conditions force the operator to lubricate and clean the machine more frequently. Usually, two types of lubricant are used: for the gearbox and for the tips of drills and drills, as well as other replaceable additives.Despite the fact that oil in a more liquid consistency is used for the gearbox.
The vast majority of models of rotary hammers, right in their instructions for use, have links to the time and period when they will require a lubricant change. The replacement process itself is carried out by pouring the substance into special holes and hatches located on the tool body and designed for pouring oils. Closing them after refilling must always meet the quality of tightness, respectively, the screw cap must not allow oil to be poured back.
Self-lubricating perforator
This process will have to be performed at regular intervals. Most professionals recommend performing this action, looking back at the manufacturer's recommendations reflected in the instructions for the tool. Thus, the frequency of the due date for changing the lubricant will depend on:
- Intensity of operation of the device;
- The volume of loads imposed on it;
- Conditions for construction work (for example, dustiness of the surrounding space).
It is recommended to change the oil immediately after changing the brushes of the electric motor. However, with the advent of experience, the operator will be able to determine by ear when the tool needs to change the oil. Before you start pouring a new portion of the oil substance, you should clarify the fact of the expiration of the warranty period for the device itself. The question is that not all models of rotary hammers provide access to the gearbox housing through a hole or hatch. And this means the need to disassemble the case, which, in the presence of a valid warranty, eliminates the latter. If the warranty has not expired, and there are no hatches, then it is better to entrust the oil change to the specialists of an authorized service center.
During self-lubrication of the gearbox, it is necessary first of all to remove the old layer. For these purposes, the crankcase is flushed with kerosene / diesel fuel (in some cases, with a “spindle”, i.e. liquid engine oil). In cases where it was necessary to disassemble the case, the mechanism is pre-purged to remove accumulated dirt and dust.
IMPORTANT! After blowing and washing the mechanisms, it is necessary to lubricate exactly those parts that were previously treated with oil, for example, a helical gear. If the element does not require lubrication, then it should not be processed (for example, a transfer clutch).
Prior to processing, the oil must be carefully prepared. The ideal lubricant for the tool will be a product released by the manufacturer of the punching equipment itself. However, this option can be far from cheap. At the same time, if it was not possible to get hold of a proprietary substance, then it is always possible to use a universal sample based on lithol (it is not bad for the Boers).
For replaceable nozzles and for drill shanks, it is better to use oil in small quantities (a drop should not be larger than a pea) and grease or lithol can serve as a lubricant. Moreover, this operation must be performed in all cases, before inserting the nozzle into the clamping chuck. After removing the nozzle, the shank must be wiped dry from accumulated dust.
IMPORTANT! The lubricant used to process the shanks must be of particularly high quality, otherwise the nozzle will easily break due to overheating or the impact mechanism may jam altogether.
Lubrication of the gearbox - the basics of the procedure
The lubricant for this element of the perforator is characterized by special requirements for the operating mode. However, this does not mean that in some cases it is forbidden to use lithol for lubrication. There are factors when, when using a domestic lubricating substance, the impact force of the tool will only increase, and the generated noise, on the contrary, will decrease.
Litol is very well suited for use in Asian-made gearboxes, because, as a rule, one does not have to rely on their warranty service. In principle, a punching tool from any manufacturer has its own design features, therefore, there is simply no standard and uniform instruction for gearbox lubrication. To complete the entire operation, you will need:
- Soft rag;
- Tool manual with manufacturer's recommendations for lubrication;
- Lubricant - either branded or universal (analogues are not welcome).
Further, on the working elements cleaned as much as possible with a rag, an oily substance is applied in an even layer. It is necessary to constantly monitor the level of lubrication so that it does not exceed the mark recommended by the manufacturer of the device. It is worth noting that lubricating the gearbox immediately upon completion of work is highly undesirable, because hot parts, when applied to them with a cold substance, can simply crack. A small amount of grease or lithol can also be applied to the drill shank. If the tool model has an open cartridge, then it makes sense to process the gland at the same time. To do this, it will need to be disassembled and wiped securely.The lubricant applied afterwards will help prolong the life of the entire instrument and will reliably prevent the spread of dust inside the case.
Requirements for oils for working elements and their types
The oil protection of various elements of the electric hammer drill may vary, depending on the different operating conditions and the prevailing combination between pressure and temperature. The application of the substance must be done with special care, because poor-quality lubrication may result in the need to replace the entire working unit.
For the Boers
Brand models of tools, as a rule, are immediately equipped with a branded container with a lubricant for use on drills. It should normally be applied to the mating bases of the liner. In this case, the viscosity parameters provided will depend on the basis used in the substance (mineral or synthetic).
Use only the brand recommended by the manufacturer. The reason is that the chemical base in this substance is specially selected for the structural materials of this model of equipment and can ensure their safety during intensive and “hot” operation. In general, this recommendation applies specifically to related products from equipment manufacturers.
For gearboxes
Gear lubrication of the perforator during its initial use will not be required, because the manufacturer has previously placed the estimated amount of oil in the body, and the manufacturer simply cannot miss this technological moment. However, during operation, the lubricant will decompose, become contaminated and, in the end, lose its useful properties.
The gear lubricant needs to be changed after some time, depending on the severity of the operating conditions and extreme overheating. Overheating is caused due to friction during the rotation of the structural elements of the device, which will be accompanied by a sharp and frequent release of liquid, which turns into vapor. It is for gearboxes that oils are used that are capable of:
- Prevent oxidation of the metal parts of the unit;
- Capture and remove various contaminants;
- Hold firmly on the surface of the protected parts;
- Do not react to excessive overheating;
- Have some ability to self-heal.
Recommended Compounds for Heavy Duty Applications
Both for drills and for replaceable nozzles, when using them during work associated with heavy loads, it is necessary to use a specific lubricant. Such compositions can be distinguished by the markings on the packaging - they are characterized by the presence of the letters "HW" ("hard work" - hard work), accompanied by an eloquent picture (the design depends only on the manufacturer). The use of universal compositions, especially if it is known in advance that hard work is ahead, is highly discouraged, because this can disable the entire mechanism of the device. At the same time, standard nigrol, grease or lithol are not suitable for such use.
A few tips to extend the life of your hammer drill
Any perforating type tool needs maintenance and routine inspection. Following a few simple rules will allow the owner to significantly increase the life of his device:
- Do not allow dust and dirt to enter the cooling holes (in extreme cases, they can be protected with an old nylon sock);
- It is preferable to treat shanks with "native" grease;
- Try not to overheat the apparatus, because in this case the lubricating substance crystallizes and ceases to perform its function;
- If the device is used in severe conditions, then the rear rotor bearing should be changed every six months, and every 70 hours of operation, the carbon brushes should be changed;
- Upon completion of making holes in the ceiling, the apparatus should be turned upside down and slightly “scrolled” it in order to lubricate the glass again on the protected parts;
- At the end of work, it is recommended to blow the inside of the equipment with compressed air;
- It is also recommended to change the rubber cartridge collar more often;
- Sparking should not be allowed on the commutator brushes during a “dry run”;
- One-time working period should not exceed half an hour;
- Do not abuse the frequent use of equipment in the "Strike" mode.
Difficulties of choice
Unlike lubricants for other types of equipment, it is easiest to select a lubricant for rotary hammers based not on the composition of the ingredients, but on the specific recommendations set out by the manufacturer of the tool in the user manual. It specifically states:
- viscosity type;
- type of water resistance;
- compatible types of lubricants;
- the possibility of using universal samples.
The question of quality in this matter depends entirely on the manufacturer. So, the products of foreign companies are very popular:
- "Makita";
- "AEG";
- Bosch;
- "Lubkon".
Slightly lower in the rating (but not always in quality) are products from:
- "Shell";
- "Castrol";
- "Ravenol".
Separately, it is worth mentioning the brand "Ultra", which is a vivid example of the "golden mean" between liquid greases.And this suggests that it can be used in both leaky and sealed gearboxes.
If, however, an equipment model is used, the manufacturer of which did not bother to give specific recommendations regarding lubricants in the instructions, then it is possible to use some of their universal types. Asian devices often suffer from such a "disease". However, they are famous for their unpretentiousness: in particular, the substance used to lubricate diesel internal combustion engines is quite suitable for them. Some craftsmen on Chinese models prefer to work out graphite lubricants. If the instrument clearly has an amateur purpose, then the domestic Litol 24 may also suit it. However, a professional tool, most likely, will not tolerate substitutes and analogues, therefore it is necessary to lubricate it only with “native” lubricant in order to prevent the risks of an uncontrolled increase in temperature and excessively sharp braking when stopped. Moreover, the use of "native" material will significantly reduce the requirements for the frequency of lubrication.
Rating of the best lubricants for rotary hammers for 2025
Samples for cartridges and drills
4th place: "ELITECH 2006"
This sample is one of the best that are presented in the lower price segment. It is extremely easy to apply to the drill shank and added to the internal cartridge part. Further, its distribution is easily carried out on the surface, which makes the protection of parts more reliable. The tool comes in convenient tubes of 60 grams, it is distinguished by economical use. The recommended retail price is 150 rubles.
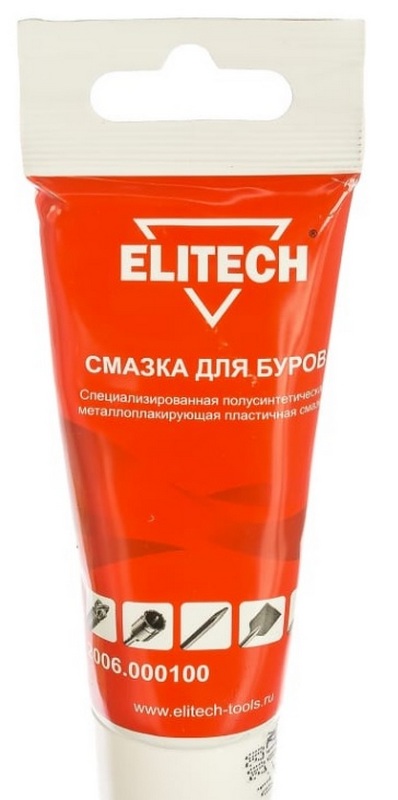
grease ELITECH 2006
Advantages:
- budget cost;
- Sufficient level of protection;
- Ease of application.
Flaws:
- Relatively short shelf life.
3rd place: "ZUBR, ZSB-125"
This sample was produced by a domestic enterprise and is perfect for equipment whose drills are used in intensive work. To do this, special additives have been added to the composition of the substance that can reduce friction as much as possible and are designed to combat excessive wear of working parts. A layer of this substance applied to the part can optimally withstand the negative effects of moisture. Has an anti-corrosion effect. The recommended cost for retail chains is 320 rubles.
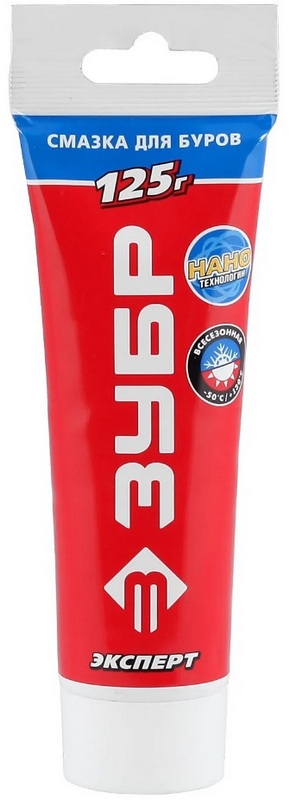
lubricant ZUBR, ZSB-125
Advantages:
- Unique nano-composition with special additives;
- Anti-corrosion protection;
- Moisture resistance.
Flaws:
- Requires frequent changes.
2nd place: PATRIOT, Arsenal AR-401
This oil option perfectly retains dust that comes from the treated surface. It is characterized by special quality and is not overly expensive. The sample is produced in tubes of small volume, however, it is spent very economically - the tubes are enough for several months of active use. The substance is intended for equipment with a rotation speed of up to 4000 rpm. Subject to this condition, the composition does not lose its viscosity, providing reliable protection against possible overheating. The recommended cost for store chains is 210 rubles.
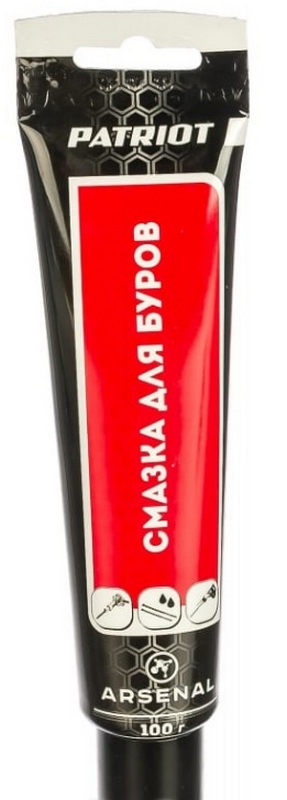
lubricant PATRIOT, Arsenal AR-401
Advantages:
- Economic consumption;
- Adequate price;
- Sufficient quality.
Flaws:
- Not suitable for every instrument.
1st place: "Metabo 6318000"
This substance is a product of the world famous German brand and is available in convenient tubes with a small volume.The sample is characterized by high quality and has a high heat resistance of the composition, and it is also capable of rapid biodegradation. It can be stored for a long time without losing its useful qualities. It is used to lubricate adapters and drills of all types. It can also be used for other inventory. The established cost for retail chains is 340 rubles.
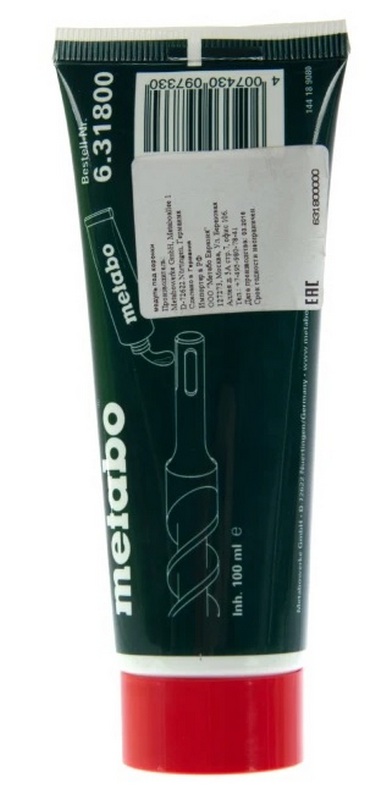
grease Metabo 6318000
Advantages:
- Increased heat resistance;
- Ability to ecological decomposition;
- Versatility.
Flaws:
Samples for gearboxes
4th place: "AL-KO reducer"
This oil stands out for its excellent German quality. It is very easy to apply on the surface of various parts and can penetrate even into very small holes. Initially, the substance was intended for garden tools, however, it can also be used for a perforator. Separately, it is worth noting the economical consumption and highly effective protection. The recommended cost for store chains is 220 rubles.
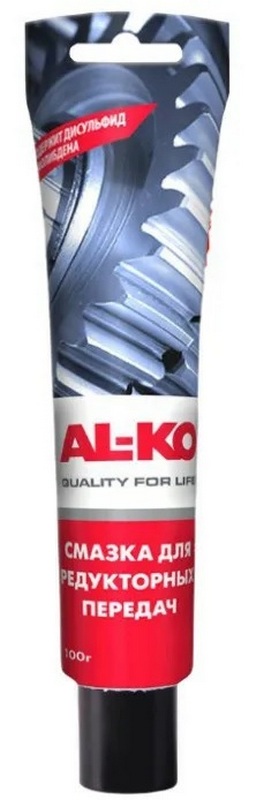
grease AL-KO redukto
Advantages:
- High efficiency;
- Versatility;
- Economic consumption.
Flaws:
- Difficult to find for sale.
3rd place: Lumberjack Grease Premium
This oil is a purely Russian product and can work with any equipment that has gears. Popularity is due to the relatively low price, good quality and the fact that the substance is firmly held on the protected surface. Can prevent excessive overheating. Among other things, it reliably captures incoming working dust. Has a wide operating temperature range. It is possible to use even on equipment operating at high speeds.The established cost for retail stores is 180 rubles.
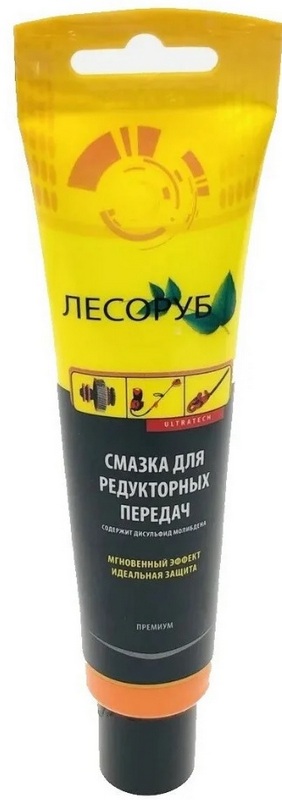
Lubricant Lumberjack Lubricant Premium
Advantages:
- Overheat protection;
- Affordable price;
- Overall efficiency.
Flaws:
2nd place: "Makita, P-08361"
This product is a product of a world famous Japanese brand. Initially, it was supplied exclusively in sets with the perforating equipment of the same name, but then, upon the discovery of universal qualities, it went on a separate sale. However, it is recommended to process only the same professional tools. It is particularly economical - 30 grams of the substance will be enough for several months. By itself, its consistency is somewhat watery, which makes it possible to penetrate into all hard-to-reach places. Not recommended for lubrication of high speed gearboxes. The established cost for retail chains is 240 rubles.
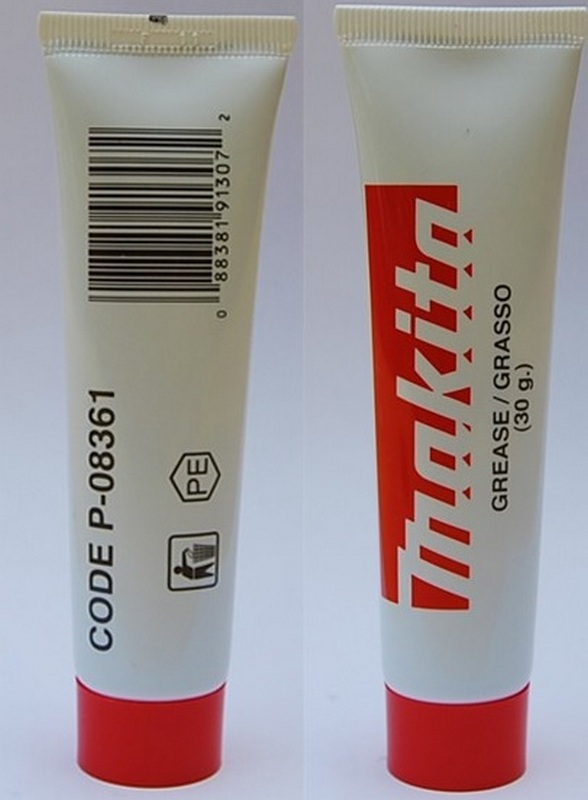
Makita grease, P-08361
Advantages:
- Adequate price;
- Good economy;
- High quality.
Flaws:
- Not recommended for lubrication of high speed gearboxes.
1st place: "VMPAUTO, ULTRA-0"
An excellent option for both professionals and amateurs. The substance is supplied in relatively large volumes (200 grams), however, it lasts for a long time. It perfectly suppresses the negative effects of gear friction, perfectly captures and removes working dust, along with small fragments of dirt. Excellent adhesion to the surface of the part, despite increased vibration. The composition is resistant to elevated temperatures and can work with almost any gear mechanisms. The established cost for retail chains is 240 rubles.
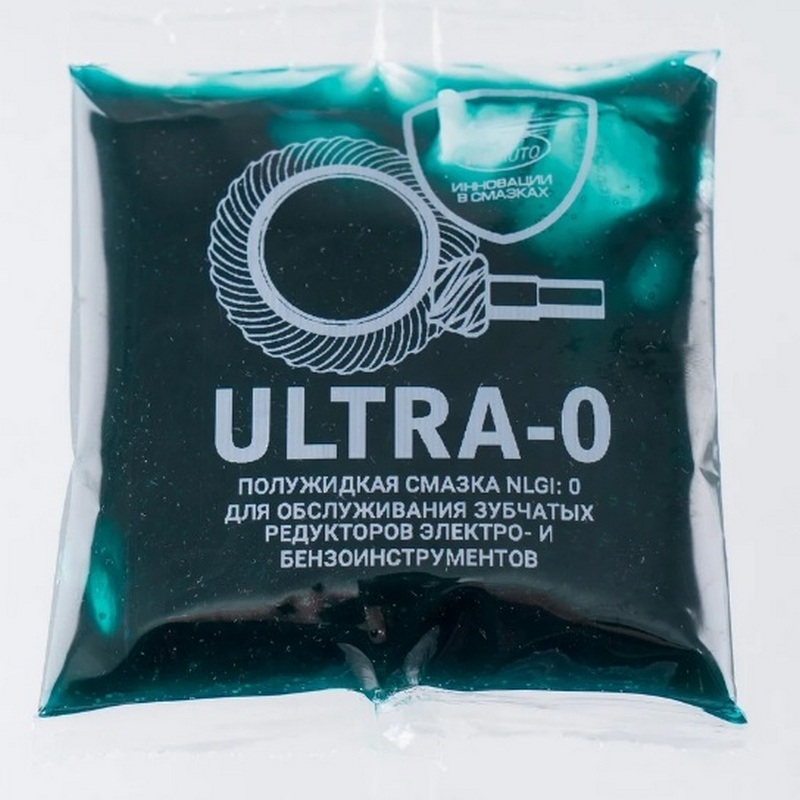
grease VMPAUTO, ULTRA-0
Advantages:
- High temperature resistance;
- Versatility;
- The best ratio of price and quality.
Flaws:
- Has a somewhat pungent odor.
Instead of an epilogue
The analysis of the market of the lubricants under consideration has established that this important element of maintenance activities for such an expensive tool as a puncher has a relatively low cost. Despite the fact that finding a quality option in today's market is not a problem. At the same time, the problem of counterfeiting products from world famous brands is acute, therefore, professionals advise purchasing lubricants in trusted online stores or trusted retail chains. Separately, it is worth mentioning Russian lubricant manufacturers, who today manage to produce completely universal options that are not inferior in quality to special foreign ones, and which have a much lower cost, and they can work with a large number of various devices.