A manual planer is a tool designed for processing wooden products (but not only). As a rule, it is used for planing, and this process involves the removal of thin layers from the top of the workpiece to a specified thickness. In this case, the mentioned thickness is determined by the characteristics of the planer. The result of the work should be the acquisition of the necessary forms by the product when creating the specified conditions of straightness and evenness. Also, the tool in question can be used to make quarters and grooves, i.e. deep recesses of various shapes.
Design features of planers
The traditional model of the tool is executed in a wooden case, in which the cutting blade is securely fixed. At the bottom there is a sole with a slot through which the cutting blade passes. For the purpose of comfortable work, a so-called horn (handle) is installed on the front of the planer, due to pressure on which the lower base is firmly attached to the surface to be treated, and at the same time the necessary direction for the knife is given. Throughout the history of use, the planer, as well as other carpentry tools, has been given many improvements. The wooden case subsequently began to be increasingly replaced with a metal one (for greater strength) or plastic (to reduce the total weight). Further, manual planing with the application of muscular effort on the part of the operator was supplanted by the use of automatic electric models. Thus, the main parts of the tool in question will always include:
- Housing - all the main components and elements of the device are fixed in it;
- Cutting knife - it is sharpened at a certain angle and is responsible for removing the wood layer;
- Clamp - provides a tight and fixed fixation of the knife in the body (can be made in the form of a metal plate or a massive wooden block);
- Chipbreaker - located just above the knife and provides a break in the outgoing chips so that it does not clog the structural elements of the device;
- Adjustment screw - this part is responsible for changing the position of the knife relative to the plane being machined.
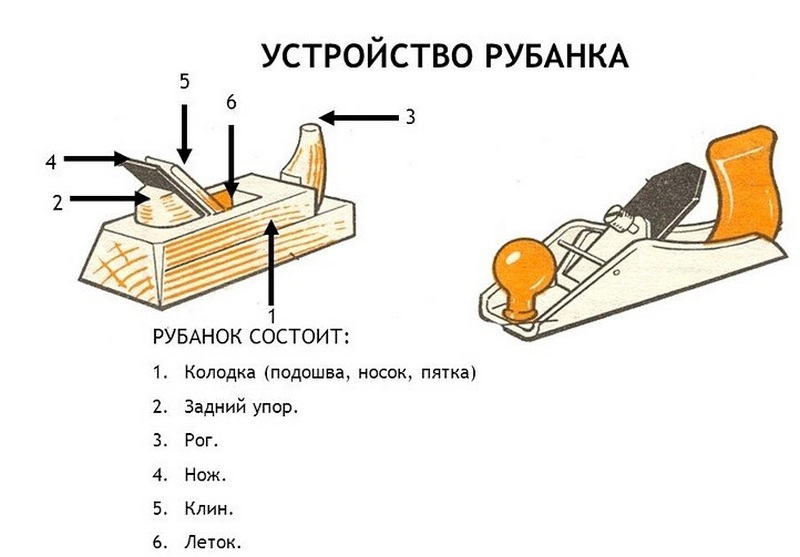
The above design has all the classic models for woodworking. However, some design elements may be missing in new samples or specialized varieties.
The principle of operation of a traditional hand planer
The main working elements of the device are its base with a guide handle and a knife. From this it is clear that the essence of his work lies in observing two parameters - this is the accuracy of setting the angle at which the knife is located, as well as ensuring a snug fit of the sole to the plane being processed.
The tightness of the working base to the surface, in most cases, will depend on the material from which the tool is made. The main condition is its perfect smoothness and evenness of the sole. The wood from which the body of the device is made will wear out and deform over time. This process can even proceed in an accelerated mode if work is carried out on a permanent basis on hardwood. In turn, a metal tool will retain the evenness of the sole for a long time, but its body may be subject to corrosion processes. Thus, when choosing a hull, it is worth relying on the conditions in which most of the work will take place.
Varieties of hand planers
The design of the carpentry fixture under consideration has several typical varieties. Even a classic manual model for professional use, with standard sizes, can be classified in terms of design features:
- Double planer - the comfort of working with it lies in the fact that it is necessarily provided with a chipbreaker, which ensures cleanliness of processing (it is more useful when finishing the product);
- Planer single - more suitable for roughing and initial surface treatment, because its knife blade is straight and single. In such a knife, the cutting edge has the smallest radius of curvature and therefore does not leave large marks behind.
In the course of their historical development, planers have had many highly specialized modifications adapted to perform a certain type of task, for example:
- Jointer - this manual type device is intended for finishing an object. A long block is its main difference from the classic planer model. It is possible to install one or two knives in such a block, which will make the work of leveling the surface more comfortable.
- Sherhebel - visually resembles the classic version, however, it has a narrower body and is necessary for making recesses. It is worth noting that with a narrow body, the tool itself has a considerable mass, and its knife is very small in width and its blade is rounded and is located at an angle of 45 degrees to the surface. This feature allows you to plan a tree across or along the grain, leaving behind in-depth recesses. Sherhebel is more used for the initial processing of wood and is designed to remove the rough top layer.
flat planing
Working with flat surfaces, for example, with bars or boards with the correct geometry, must be carried out with a high degree of accuracy. Deviation from the standards of straight lines can radically change the dimensions and dimensions of the material. For this type of work, the following devices with a special design are used:
- Semi-joiner - unlike the classic jointer, it has a small knife and sole. This feature allows you to work with both large and small workpieces, while maintaining the evenness and straightness of the surface, without losing the quality of accuracy;
- Zinubel - this tool gives the surface a rough effect, which is necessary for better adhesion between objects when connecting them with glue. The device is equipped with a blade with teeth and it can even cut serrated wood and the ends of objects.
Figure planing
Figured planing on wood is a whole art. To create unique products with a profile section, it is necessary to use a special material - wood of the highest quality, which should have a minimum number of knots, and it should be straight-grained. At the same time, such high-quality material must be processed with a special-purpose tool. Such tools may include:
- Kalevka - this type of planer is used for figured processing of objects. It has a sole with several levels and special edges on the knife. Perfect for making carved door/window architraves, baguettes and cornices.
- Tongue-and-groove - used for making grooves, holes in boards and tongue and groove joints, as well as other joints of the "groove-thorn" type. Consists of fixing and guide pads held by screws.
- Gruntubel - it is designed for cleaning grooves in the form of a trapezoid along the wood fibers.
- Zenzubel - it is used to make grooves and quarters with their subsequent cleaning. The knives of this device are shaped like blades, and the body is equipped with a special hole for dumping chips.
- Falzgebel - used for stripping and selecting quarters, has a stepped sole.
- Gorbach - its plantar base has a convex shape, which is very convenient for working with cylindrical, semicircular or concave surfaces.
Knife blade adjustment and sharpening
Proper adjustment of the position of the cutting knife will reduce the time and muscle costs for processing the object. The rib, which is the working surface of the blade edge, has a slight radial rounding. In order to reduce it, it is necessary to sharpen the blade in several steps using a grinding wheel or a fine-grained grinding stone. A sharpening angle of 30 degrees is considered universal and is ideal for working with both soft and hard materials.
In turn, if the blade simply slides over the surface, then this means that it does not protrude enough. If the blade is extended far from the block, then it will remove too thick a layer and tear the wood fibers. From this it is clear that the working part of the knife should protrude from the body by no more than 0.2 to 0.3 millimeters, and this will ensure the proper requirements for uniformity and parallelism. Such an adjustment can be carried out both “by eye” and with the help of a ruler, by adjusting the length of the knife extension with a hammer or a retractable screw.
Naturally, a hand planer, like any other carpentry tool, requires constant care.No matter how excellent the quality of steel used to make a knife is, sooner or later it will become dull and will need to be sharpened. As a rule, sharpening is performed on a special stone called a whetstone. To do this, its (stone) surface is moistened with water, and the blade itself will also have to be sprayed during turning. To get the best possible effect, the blade should be pressed as tightly as possible against the stone. You can choose the sharpening angle yourself, but 30 degrees are considered the best option. Before starting the process, you should pay attention to how the blade was originally sharpened and it is advisable to repeat this procedure. For example, some professionals prefer to sharpen a knife not on a whetstone, but on a grinding wheel. If a similar procedure was used, then when using a whetstone, the blade should be applied to the side surface, and not to the edge. Sharpening with a wheel will only achieve maximum results if its abrasive surface is fine-grained. Otherwise, it will be necessary to fine-tune with fine sandpaper or a whetstone. The quality of the work done can even be assessed "by eye" - if the blade does not shine, then the knife is sharpened with high quality and can be used.
Basic rules for working with a hand planer
This tool should only be used in accordance with its design features. During planing, muscular force is transmitted to the front of the body by the user's left hand, while the back is held by the right hand. It is important to carry out the planer along the fibers with measured and translational movements.The main point in finishing is that you should not reduce the force applied to the planer and do not remove it from the product without completing a one-time pass. But for roughing, small and frequent movements are quite suitable. The main sign of high-quality processing will be a continuous belt of wood shavings coming out from under the tool blade. Although it may seem that the planing process is quite simple, extra training will not hurt. So, in the production of the final processing of the product, it is worth first practicing on substandard materials (trimmings and stumps), because there is a risk of damaging the workpiece with deep unnecessary cuts or hooks. The basic safety rules can be reduced to several provisions:
- Before starting work, you need to check the serviceability and accuracy of the planer settings;
- The device must be stored in a special place with the right conditions;
- During operation, the user's body must maintain a stable position, and the hands must be safe;
- Upon completion of work, the device should be cleaned of chips.
End cleaning rules
When cleaning the ends of the product, the planer moves in the direction "from itself", with short jerks. This processing method will allow you to cut the wood fibers across with less muscle effort. To avoid chipping on the edge, it is required to initially chamfer. In general, it is even better to process one end to the middle, then process the butt from the other end to the middle too.
Possible mistakes when working with a manual planer
- Before starting work, you should carefully consider the direction of the wood fibers on the board. They should be directed according to the degree of removal of the device from the user's body.In cases where this requirement is not met and the work is carried out with a planer towards the fibers, the result can be a much rougher and less accurate result.
- Also, a situation is possible when the processed material is poorly dried and twisted with a “screw”. Such helical winging and helical warp are eliminated by chiselling raised corners on all sides. The final alignment can be done during finishing.
- The main problem when working with ends is the creation of so-called “flakes”. Their occurrence can be avoided by planing from the edges to the middle, alternately alternating the processing side.
- An unpleasant situation is possible when, after planing, the surface of the product remains convex. This can happen if, starting from the edge, the planer is involuntarily held almost in weight and at an angle. Avoiding this problem is very simple - you need to constantly monitor the correctness of holding the planer in the desired position;
- When finishing the product, you should press a little harder on the body, while advancing the tool exclusively with your right hand. The left one will guide him forward. This shows that it is necessary to apply great efforts to that part of the device that is currently located directly on the workpiece. And the pressure on the part that is in the air, on the contrary, must be reduced. Following this rule will allow you to get a smooth and well-treated surface.
Difficulties of choice
When buying a planer, you should first of all pay attention to the quality of the knife - the efficiency and productivity of future work will depend on it.This element must be made of quality steel, and it must work for a significant period of time without the need for sharpening. Visually determine the quality of the knife material, of course, is quite difficult. Thus, it is worth paying attention to the reputation of the manufacturer's brand. The next step in the test will be to determine the stability of the blade in the body - in no case should it stagger. The handle should also be given special attention - its position must be stable, and it itself must hold firmly on the body. Additionally, it will not be superfluous to check the following parameters:
- The sharpening angle is one of the main criteria that will determine the quality of wood processing and the speed of work. An excellent bonus will be the option, thanks to which the body design provides for a mechanism responsible for setting the sharpening angle.
- The sole - it is also able to influence the final result of the work. The sole must be as smooth as possible in order to ensure proper evenness of the surface of the workpiece.
- The thickness of the removed chips - this parameter can be adjusted with a special screw on the tool, which is responsible for the depth of the blade extension. Sometimes, next to such a screw, there is a marking bar that clearly shows the specified thickness.
Rating of the best hand planers for 2022
Budget segment
3rd place: STAYER TOPCut
A very simple and small device, made according to classical technology. The handle and body are made of solid wood. The sample is well suited for both roughing and finishing work on smooth wood surfaces.There are a number of shortcomings, such as insufficient strength of the case, however, all this is more than offset by a very budgetary cost. The recommended price for store chains is 410 rubles.
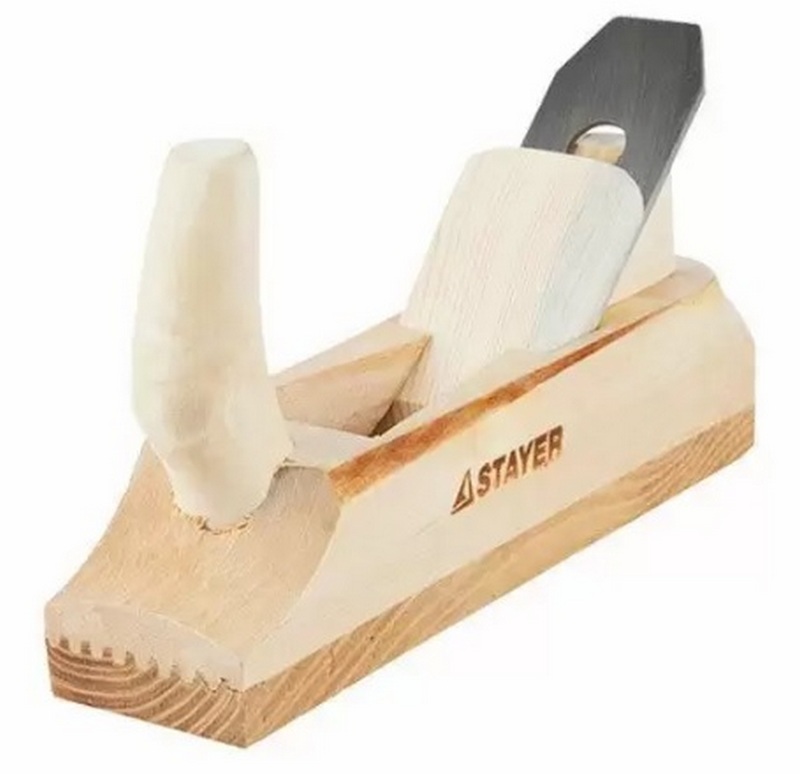
planer STAYER TOPCut
Advantages:
- Budget price;
- Organic material of manufacture;
- Classical production technology.
Flaws:
2nd place: "Biber 85071"
Another simple model. The main area of application is high-speed and rough wood processing. The body is made of steel and has additional stiffening ribs. The handle is made using ergonomic technology and is as comfortable as possible when working. The blade and knife (their positions) are adjusted using a special screw. The smooth outsole makes it much easier to move even on rough surfaces. The recommended cost for a retail network is 530 rubles.
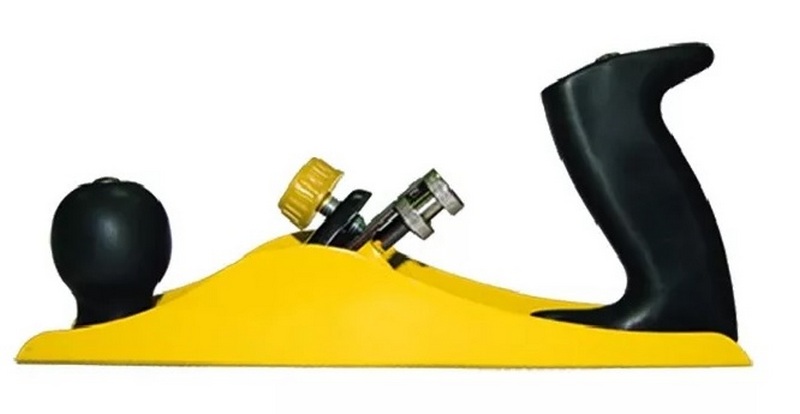
Biber 85071
Advantages:
- budget cost;
- Orientation to work with rough wood species;
- Blade adjustable.
Flaws:
1st place: "FIT 43714"
A standard type of tool designed for use in the carpentry industry. The body is made on a metal base, and the blade is made of alloy steel, which together provides an extended tool life. At the same time, its wear resistance is also increased. Due to its small dimensions and weight, this planer is easy and uncomplicated to use. The established retail price is 900 rubles.
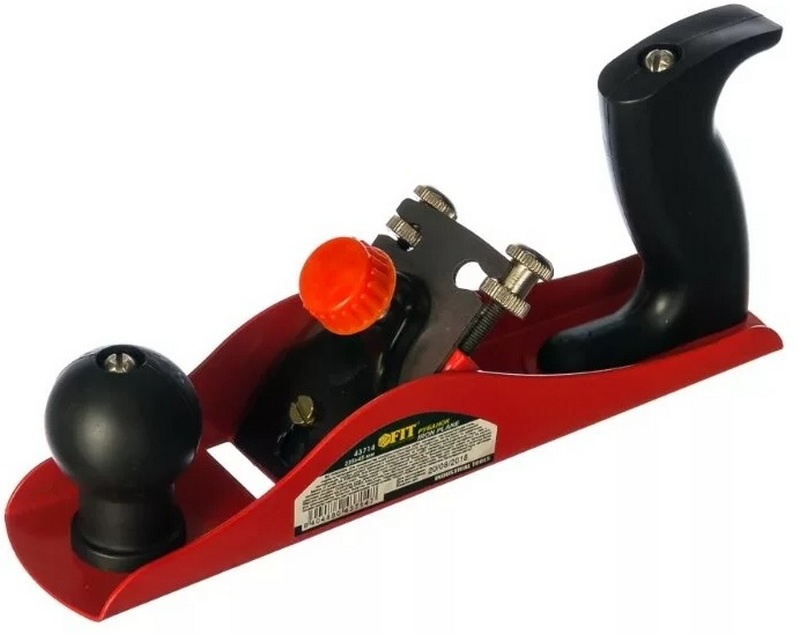
FIT 43714
Advantages:
- Lightweight and small tool
- Metal case;
- Extended service life.
Flaws:
- Some fasteners raise questions.
Middle price segment
3rd place: "Sparta 210795"
An excellent tool for planing excess wood from wooden blanks in order to obtain smooth surfaces. Especially well copes with work in the conditions of the constrained space. The case is made of high-strength materials and does not deform even under significant operating loads. The design of the tool provides the option of self-centering of the cutting blade. The body has a built-in chipbreaker. The recommended cost for retail chains is 1100 rubles.
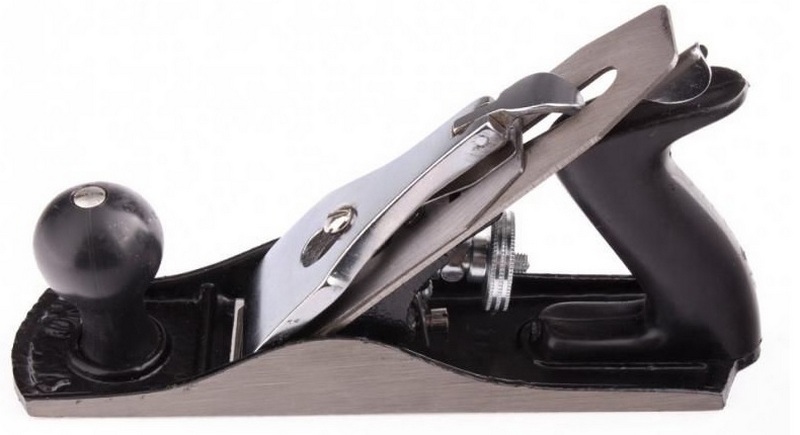
Sparta 210795
Advantages:
- Small dimensions and weight;
- Ability to work in confined spaces;
- Adequate price.
Flaws:
2nd place: "ZUBR Expert "Single"
A simple and reliable tool made according to the technology that was adopted back in the days of the USSR. Differs in special reliability at operation. It is more designed for primary processing of wood than for finishing. As a standard, the sole of the device initially has some concavity, which, if not necessary, is simply removed by the grinding procedure. Knives are perfectly sharpened on any grinding device - from a whetstone to an abrasive wheel. The blade itself has special roundings on both corners. The established store price is 1500 rubles.
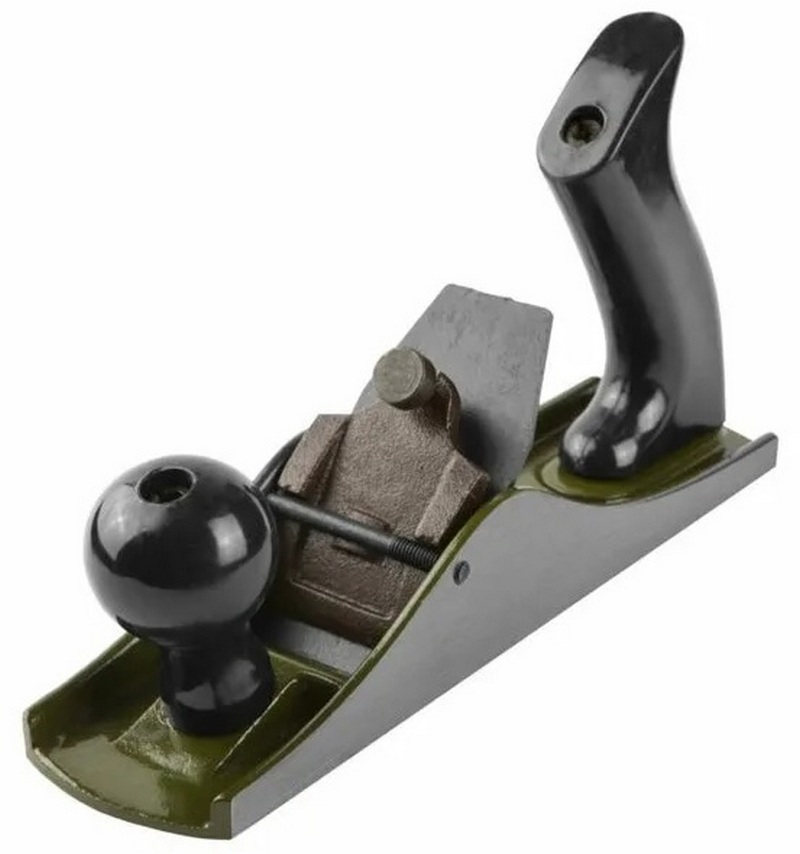
ZUBR Expert "Single
Advantages:
- Excellent geometric shape;
- Reliable knives;
- Curved blades.
Flaws:
- The need to refine the sole.
1st place: STANLEY 60 1/2 1-12-060
This model is produced by a world famous brand. The main purpose is the processing of ends. Perfect for all types of wood, including the hardest.In order to more accurately adjust the knife, the device is equipped with a special mechanism for setting the working angle. All planer elements are made of durable metal, which significantly expands the time limits of its operational life. The handles are ergonomically designed for a comfortable working grip. The recommended store price is 2700 rubles.
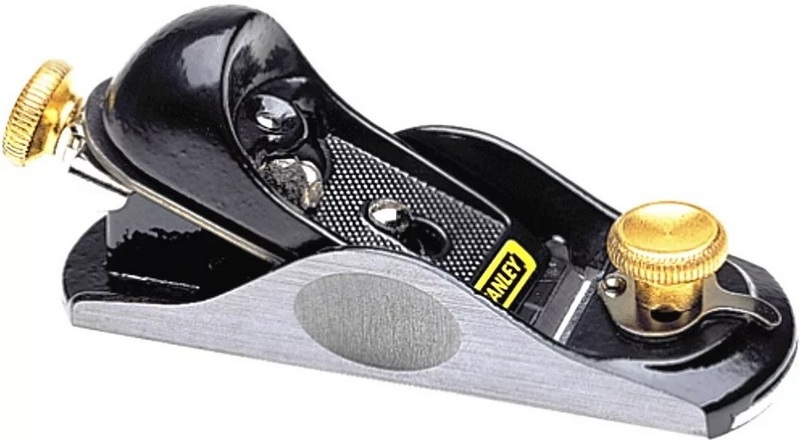
STANLEY 60 1/2 1-12-060
Advantages:
- Ergonomic design;
- Precise adjustment of the working angle;
- Ability to work with various types of wood.
Flaws:
Premium class
2nd place: "Irwin T06012"
This end tool is rightfully considered a model of high quality. The body is completely made of strong metal and at the same time is unusually light. All these qualities ensure high performance. The blade of the knife is made of high quality carbon steel and can work for a long time without sharpening. The set price for retail chains is 7,700 rubles.
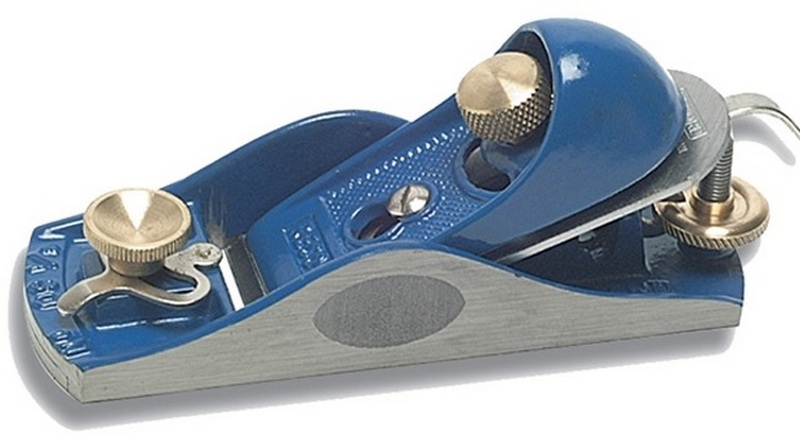
Irwin T06012
Advantages:
- Rugged housing;
- Reliable knife;
- Great performance.
Flaws:
1st place: "Kraftool 18527-35"
An excellent multi-purpose planer model. Ideal for both primary and finishing applications. Also, this planer is able to qualitatively process fiberboard and chipboard, drywall and plastic. The blade has a large set of cutting edges, and the issued chips are reliably removed. The alloy used for the manufacture of the case is resistant to mechanical stress. Recommended retail price - 9000 rubles.
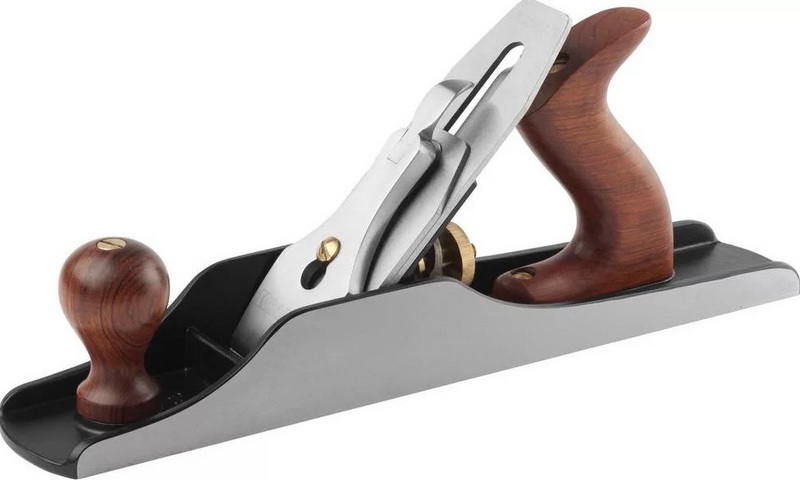
Kraftool 18527-35
Advantages:
- Reliable body alloy;
- Ability to process a variety of materials;
- The knife has many cutting edges.
Flaws:
Instead of an epilogue
The analysis of the market of the instruments under consideration established that the majority of positions on it are occupied by foreign-made goods. Rare models from domestic brands are able to penetrate only the middle price segment, and then thanks to high-quality manufacturing technology that has been established since Soviet times. However, foreign brands (even from the budget segment) can boast of the quality of workmanship and the possibility of effective use for most typical carpentry tasks. As for the premium class, it presents extremely expensive and reliable devices, which, although they cost a lot, are fully capable of working out their price. As a vivid example, one can cite the fact that in the premium class there are practically no models made of low-quality steel or those in which the knife requires frequent sharpening.