A significant amount of turning work is carried out by means of special cutters. In terms of frequency of use, cutting tools occupy one of the leading places among these nozzles. They are a type of turning tool designed for cutting deep and narrow grooves in blank objects. Such models, as a rule, are used to remove an already processed workpiece from a bar that was fed through a spindle hole. Due to the special specifics of their cutting edge, cut-off samples differ significantly from their counterparts: threaded, through-hole, boring and other types of cutters.
The cut-off operation does not take up such a large part of the working time compared to the total time spent on processing the part, however, it is often the last one in the general list of the work cycle, which is due to the provision of high-quality processing of the end face of the workpiece. Incorrect selection of the sharpening angle on the cutting plate significantly increases the risk of chips and roughness on the cut surface, which, in turn, will lead to the rejection of the product or make it impossible to further process it. One of the main features of a cut-off turning cutter is that its frontal part, during operation, plunges into a narrowed groove, whose size in diameter is slightly larger than the width of the cutting edge blade. This circumstance creates some difficulties for the removal of waste chips and for the cooling process of the nozzle, which requires the use of non-standard working solutions.
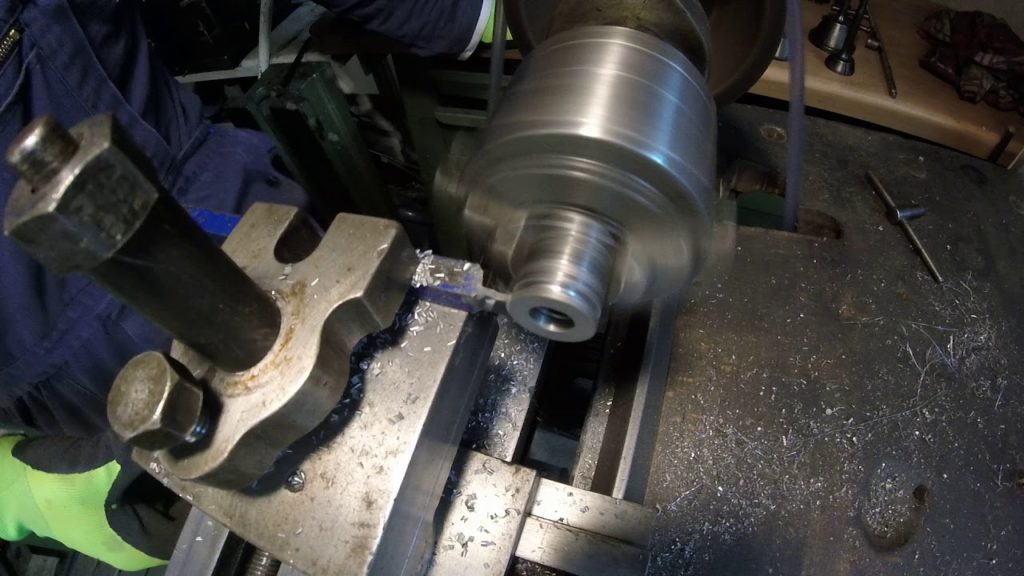
Design features of the cut-off cutter
He himself is a monolithic all-metal turning tool, consisting of a flat head and a massive holder. There is a cutting plate at the end of the head. In comparison with other types of turning nozzles, in addition to the main cutting edge, the cutter also has two auxiliary ones, located on both sides of the main one, intended for cutting surfaces on the side of the slot being cut. The cutting head blade becomes narrower when moved towards the holder at angles of 1-3 degrees for each side. This design feature is required in order to be able to reduce the friction of the nozzle against the walls of the groove, as well as in order to improve the circulation of the cutting fluid and the ejection of chips.
The width of the blade head can range from 3-10 millimeters, and its length should be selected in such a way as to be a few millimeters larger relative to the radius of the workpiece. In order to increase the strength and reduce the level of vibration, it is necessary to use special types of cut-off cutters, in which the front part is enlarged. Such a tool will be given a qualitative balance by heads that have rounded protrusions on top (they are also called “cockerels”), and which will make it possible to place the cutting edge on the same line as the axis of the holder.
Types and scope of cutting cutters
Structurally, the nozzles under consideration are divided into prefabricated and monolithic (all-metal).The latter are made from heavy-duty tool steel, and their main technical characteristics are regulated by the State Standard No. 18874 of 1973. The maximum dimensions of such a cutter are:
- Full length - 80 millimeters;
- Head length - 15 millimeters;
- The width of the cutting edge is 12 millimeters.
IMPORTANT! As the incisal edge is ground down, the head length of this tool will decrease, which, accordingly, will lower the cut-off diameter limit.
Prefabricated models, in turn, can be divided into two types. The first type looks like a monolithic sample, in which both the head and the holder are made of a single bar, but the cutting plate is a separate prefabricated element installed on the end of the head. Its fastening can be done in two ways - either by soldering to the base, or by mechanical fastening.
The second type of prefabricated model has become the most widespread in the modern world of assembled incisors. It has a long and flat head with a cutting edge, which is mechanically fixed in a special frame, which acts as a kind of holder. These cutters are sold with interchangeable inserts that vary in thickness and width. Among other things, some of the described samples are able to adjust the ejection length of their head.
In addition to the reinforced and standard versions of the cutting nozzle in the classic design, other types of cutting tools can be used to work in special conditions, which can compensate for the low rigidity or low power of the lathe. This includes inverted or spring models, often used in small-scale production or in household workshops.Their heads can compensate for dynamic shock loads and absorb (as far as possible) the generated vibrations, and this will achieve the desired surface quality and protect the cutting edge from damage.
IMPORTANT! The popularity of inverted models came about five or six years ago, due to the fact that an effective and easy-to-use cutting insert was developed.
Inverted cutters - specifics and advantages
This type of cutting equipment is called so because it works counterclockwise, i.e. on the reverse movement of the spindle. Its design is somewhat similar to a clerical knife: a plate in the form of a long blade and a holder are fixed on an oblique end. The blade is made of high-speed steel, which is alloyed with cobalt, and in cross section it is visually represented as the letter “T” turned upside down, in which both crossbars are, as it were, shortened. The sharpening angle of the end of the cutting edge is seven degrees, the manufacturer can produce tools in different thicknesses from one to three point two tenths of a millimeter.
The main advantage of the cutter under consideration is the facilitated removal of chips, because when the spindle is rotated in the opposite direction, the chips, under the influence of their own weight, are thrown down. This mode significantly reduces the likelihood of filling the working groove with spent chips, which means that there is almost no risk of machine breakdown or jamming. Additional advantages of such a nozzle include:
- Ease of sharpening blades;
- Possibility of processing at an increased reach;
- Optimization of the cooling process (chips go down, and coolant is supplied from above);
- Possession of a long service life even with repeated regrinding of the cutting insert.
Among other things, the inverted cutter has a point height adjustment system, which makes the need to adjust the position of the nozzle in position when using gaskets is simply unnecessary.
Applied marking
In the Russian Federation, there are three state standards (GOST), which were developed back in Soviet times and have been in force since 1973 (they have the index “73” at the end of the digital name of the document) and which are designed to establish regulations for marking cutting tools. The coding of nozzles and their standard sizes made of high-speed steel are established by the standard No. 18874; nozzles with hard-alloy plates - standard No. 18884; having curved plates ("cockerel") carbide - standard No. 18894. It is simply impossible to properly establish the geometry and type by marking without using the technical tables of these standards. In all three listed regulatory documents, each type has its own code and the number of parameters indicated in the tables. The only decipherable informative element of the marking is the classification of the alloy of the cutting part. For example, a right cutter made of high speed steel has the following characteristics:
- Cross section - 16x16 millimeters;
- Length - 80 millimeters;
- Head - 15 millimeters;
- Blade width - 12 millimeters.
The above parameters according to standard No. 18874 will have the general marking "2120-0519". A cutter with similar geometry, but with a carbide insert, will be marked based on standard No. 18884 as "2130-055 T5K10". The last alphanumeric set means the presence of titanium carbide with cobalt in the carbide composition, where 10 is the percentage of the latter.For more information, some manufacturers specifically highlight the type of material used in color. For example, the above "T5K10" is yellow.
There is also a universal international system in the world for designating cutting tools in ISO (International Organization for Standardization) gradation. The corresponding document of this organization is very voluminous, contains many characteristics, so the full marking seems to be quite long. As an example, the transcript "QFGD2525R2252H" in the category "Grooving and external cuts" can be given, where:
- Q - cutting holder;
- F - end processing;
- G - dimensions of the plate;
- D - for double-sided plates;
- 25 – holder height;
- 25 – holder width;
- R - left, right, neutral;
- 22 - maximum working depth;
- 52 - minimum cut-in diameter;
- H is the insert position for face grooving.
Benefits of using carbides in cutting inserts
The main advantage of a carbide insert over its high speed steel counterparts is that it has the ability to operate at high cutting speeds (up to 500 m/s for steel blanks). Moreover, while maintaining its own hardness at a general high temperature in the working area (up to 900 degrees Celsius). As mentioned above, there are two methods for attaching carbide inserts to the holder head - mechanical clamping and soldering (or other similar methods). Connections that are one-piece are considered more resistant to vibrations and are generally structurally simple, especially when working on intense loads.However, despite the technically complex production method, the cut-off tool, on which the plate is mechanically fixed, has a number of advantages:
- When working on the head of its holder, there is no thermal effect when the cutting element is fixed;
- A quick reversal to another cutting edge or an accelerated insert change is available;
- After changing the insert, the geometric characteristics will be preserved.
In addition to cutting carbide parts, when working on especially hard metals, it is possible to use inserts based on ceramics. Although they are considered more fragile, they have increased wear resistance of the cutting part and are able to work at very high temperatures formed in the working area (up to 1200 degrees Celsius).
Recommendations for choosing cutting tools
Production technology
When buying the type of cutters in question, more attention should be paid to the requirements of state standards used by the manufacturer in production. The question of a small price should not occupy a dominant position. Thus, incisors, the manufacturing technology of which cannot be confirmed, are unlikely to be able to last for a long time, and it will be problematic to sharpen them. The simplest sign of inconsistency in tool production technology is its very cheap price. It should always be remembered that only goods produced according to state standards will be able to provide a technological work cycle without interruptions.
Criterias of choice
You need to know that cutters are highly specialized nozzles and should be used for two operations only - turning and cutting. Thus, for small repair facilities and domestic use, you should not purchase overly expensive and professional samples.In this situation, it is quite possible to get by with a Russian-made sample with a brazed plate, the cost of which will be 1.5-2 times lower than that of a similar one with a mechanically fastened carbide plate. At the same time, this rule does not apply to mass production, especially if the cutter will be used on CNC machines. There is simply no alternative to a high-tech cutting model with an interchangeable insert.
Summing up, it should be noted that before the acquisition, a potential buyer needs to decide on the following points:
- Calculate the intensity of future loads;
- Take into account the hardness of the material being processed;
- Consider the types of future work;
- Set the priority between the parameters of the desired surface quality and the accuracy of the dimensions of the product;
- Adopt the desired degree of wear resistance of the tooling.
Workflow Basics
Sharpening of cutters - general recommendations
The efficiency of the cutter, as well as the cutting force and the overall service life, directly depend on high-quality sharpening. For turning equipment, it is customary to sharpen both of its edges. The grinding is carried out in several steps, separately for each working cutting surface. The process starts from the back - the operator must work the back surface at about a 5-degree angle. Next, you should grind the back plane of the cutting edge. The angle to be sharpened for the back insert should exceed the clearance angle of the cut by about two degrees. After turning the cutting and rear parts, the operator must form the final cutting angle by finishing. The front part should also be turned according to the algorithm described above.It is worth remembering that the angle on the front of the cutter must be created by double turning or by finishing. The working edge along which the grinding is carried out must be located on a parallel straight line with the grinding surface.
Installing the cutter
In order to properly perform the cutting procedure and in order to stop increased wear of the cutting insert, as well as to ensure high-quality end face processing after cutting, it is worth setting the cutter in a completely perpendicular position with respect to the workpiece. In addition, it should be installed opposite the rotational axis, with vertical deviation no more than 0.1 mm in both directions. Placing the cutting edge even a small fraction of tenths of a millimeter higher can lead to blade breakage, and with a lower setting, an uncut ledge can form on the workpiece. Cutting should be carried out as close as possible to the jaws of the chuck, using a cutter with a minimum overhang. For comfortable machining of hard materials with bench-top machines, inverted or spring-loaded tools should be used.
Rating of the best cutting tools for 2022
Budget options
3rd place: Tekhnostal 2130-0001 036258
Standard sample with right hand feed. It has a total length of 100 millimeters with a holder length of 10, and its height is 16. Made of T5K10 material - interspersed with carbide. The country of origin is China, the recommended retail price is 185 rubles.

Technostal 2130-0001 036258
Advantages:
- Production material interspersed with carbide;
- Sufficient length;
- Cutting edge soldering.
Flaws:
- Requires initial roughing.
2nd place: "Sekira 1781"
Another representative of the budget group, made of reinforced material T5K6 (small titanium inclusions). It has a total length of 140 millimeters, with a holder height of 25 and its width of 16. The country of origin is China, the cost in retail chains is 205 rubles.
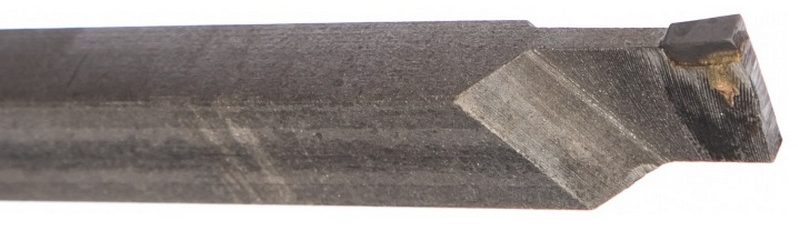
Sekira 1781
Advantages:
- Inclusion of titanium in the material of manufacture;
- Long base;
- budget cost.
Flaws:
- Requires initial sharpening.
1st place: Tekhnostal 2130-0005 030431
This cutter is made of ordinary superhard steel grade T5K10 with carbide impregnation and has a brazed cutting tip. The overall length is 120 millimeters, with a holder height of 20 and its width is 12. Produced in China under a Russian license. The price in retail stores is set at 220 rubles.

Technostal 2130-0005 030431
Advantages:
- Good geometric data;
- High speed steel used;
- Soldered tip.
Flaws:
- Again, the need for initial sharpening.
Middle price segment
3rd place: TekhnoStal 036377
This turning tool is distinguished by its extended geometric characteristics, the base is made of an alloy interspersed with titanium. It has a total length of 170 millimeters, with a holder width of 20, and its height is 32. Made in China. The recommended price for the store is 310 rubles.

TechnoStal 036377
Advantages:
- Reasonable price;
- Excellent geometric dimensions;
- Titanium insert.
Flaws:
2nd place: "Sekira 15125"
A good option from the Belarusian manufacturer for the right feed. The body is made of high speed steel with carbide inclusions. It has a total length of 140 millimeters, and a holder height of 25, and its width is 20.Country of manufacture - Belarus. The recommended retail price is 410 rubles.

Sekira 15125
Advantages:
- Good geometric characteristics;
- High speed steel material;
- Adequate value for money.
Flaws:
1st place: "Sekira 18917"
Leading model for its segment. It is made of heavy-duty R6M5 steel and has the following geometric characteristics: overall length - 125 millimeters, holder width - 4, holder height - 18. Due to its special geometric parameters, it can be used for small almost jewelry work. Country of manufacture - Belarus. The price set for stores is 520 rubles.
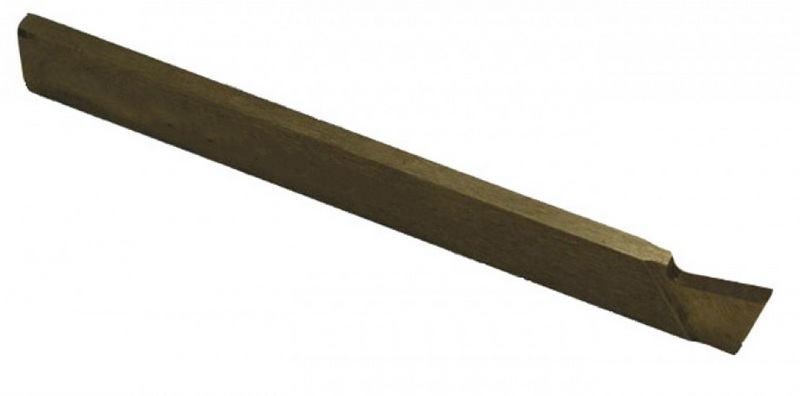
Sekira 18917
Advantages:
- Designed for precision work;
- Use of innovative material;
- Real price.
Flaws:
Premium class
3rd place: "MGEHR1212-2"
An excellent and multifunctional model used with interchangeable cutting inserts. Differs in the high durability and long operational term. Made from quality material. The country of manufacture is Russia, the recommended retail price is 900 rubles.
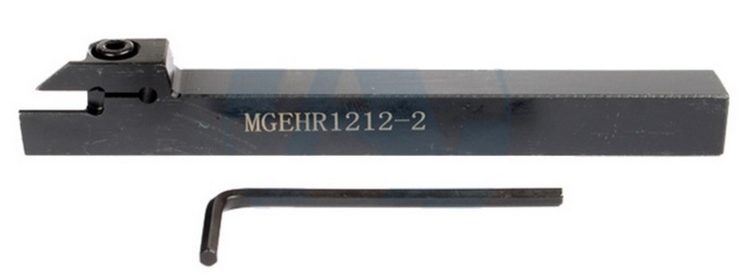
MGEHR1212-2
Advantages:
- Possibility of using various cutting plates;
- High-quality execution of grooves and cuts;
- Multifunctionality and versatility.
Flaws:
2nd place: "24554 Proxxon"
A highly practical foreign-made tool, excellent for cutting grooves and cutting off materials. Manufactured from high speed steel with cobalt content (hardened). Suitable for lathe PD-400. It has dimensions - 12 x 3 x 85 millimeters. Country of manufacture - Germany. The recommended price for retail chains is 1300 rubles.

24554 proxxon
Advantages:
- The manufacturer is a world famous brand;
- High-quality case material;
- Long service life.
Flaws:
1st place: "Jet 50000909"
This sample is suitable for work on JET BD-7, 8 and 920 machines. It is intended for cutting material at an angle of 90 degrees to the rotational axis and for cutting very narrow grooves. Able to work under heavy loads, may require cutting technology with great accuracy. When working with it, do not exceed the feed rate! Dimensions - 150 x 8 x8 millimeters, Country - manufacturer - Switzerland. The recommended price for shops is 2300 rubles.

Jet 50000909
Advantages:
- High-quality manufacturing material;
- Ability to spot work;
- Withstanding intense loads.
Flaws:
- Necessity of exact observance of feed rate.
Instead of an epilogue
The analysis of the cutter market found that for domestic needs, the Russian buyer, like a small entrepreneur in the field of turning, most of all prefers inexpensive tool samples located in the lower price segment. Such models have soldered cutting edges, require the original, but are extremely cheap in price. It is worth noting that even Russian manufacturers have transferred the technology for the production of such nozzles to Asia - most of the popular cutters are produced either in Asian countries or in neighboring countries under Russian licenses. At the same time, the premium segment, which is focused on mass production and requires special endurance due to intense loads, is represented exclusively by samples from Western Europe.They are distinguished by high quality, they cost 3-5 orders of magnitude more expensive, and most often these are multifunctional and universal models.