Planer for wood processing (joiner) - special equipment designed for sawing and planing wooden blanks. With it, it is possible to create one or more basic surfaces on a bar. The machine is used for construction, repair and finishing works.
Design
The design of the machine in question includes the following parts:
- Motor powered by 220 volts. An electric motor generates and transmits "torque" to the cutterhead with knives.
- Working table consisting of front and rear plates (made of cast iron and have special stiffening ribs, due to which the stability of the working surface is ensured). The edges of the tiles are provided with special stainless steel overlays that protect the work surface from mechanical damage. The back plate is installed at the same level as the cutting blades. The front plate is located 2 mm below the rear. The distance between them varies, depending on which layer of material you want to remove from the workpiece.
- The bed, which is made of very durable alloys. This element supports the entire mass of the machine, and must also withstand the forces that the operator applies to press on the workpiece. It also contains shafts with knives, guide parts and other fasteners.
- A cutterhead mounted between the front and rear tiles. Attached to this shaft are blades of equal thickness, made of high-speed tool steel.In the case when it is necessary to process hardwood material on the machine, the shaft must be additionally equipped with carbide tipped.
- Guide - this element is a node that is responsible for moving the moving parts of the equipment and the workpiece itself. The guide is bolted to the frame and can move in a transverse direction.
- The circular guard is placed on the front tile and must fit snugly against the guide. This guard is made of sheet metal and provides protection for the knife shaft.
IMPORTANT! As a rule, planer equipment is allowed to process parts with a length of 1 to 1.5 meters. Parts with a longer length are inconvenient to fix on the working surface of the table, they can be deformed, and in this case, the accuracy of the cut may noticeably decrease and in general there will be a general inconvenience in work. But processing parts with a length of less than 1 m is generally traumatic.
Operating principle
The complete procedure for the operation of the equipment consists of the following steps:
- The rear tile remains stationary throughout the entire production process. The location of the front tile is adjusted by the operator to the required height.
- After turning on the machine, the electric motor transmits revolutions to the knife shaft, as a result of which the cutting parts begin to rotate.
- The wooden blank is applied to the guide element (ruler) with both hands and directed to the cutters (knives). If the machine belongs to budget models, then the feed on it is carried out only manually, and this is traumatic.However, most modern machines are already equipped with an automatic feeder, which increases the speed of sending parts and ensures the overall safety of the production process.
- When the workpiece gets under the knives, they remove the thickness of the layer determined by the operator from the wood, while eliminating irregularities and creating a clean and flat base surface. The speed of execution will directly depend on the planing technology. Most planer machines can only process one surface in one pass, but planers already exist that can process two sides at the same time.
In the case when, upon completion of processing, small irregularities or fibers form on the surface, this indicates that the knife blades need to be re-sharpened. If the irregularities are large, then the distance between the tiles and the cutterhead must be properly adjusted.
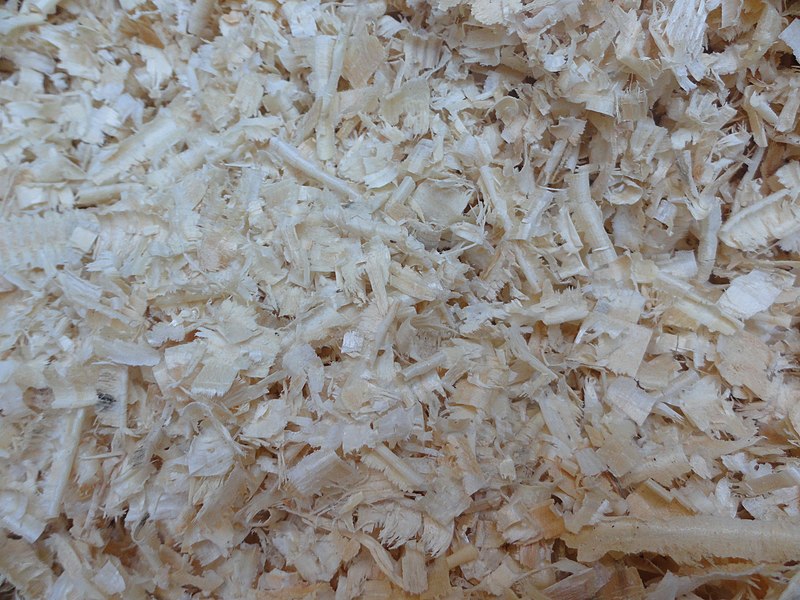
Scope of application and advantageous features
Jointing equipment is used for the following production operations:
- Leveling surfaces on large wooden bars;
- Rough trimming of workpiece planes;
- Angular grooving;
- Removing edges.
Unlike other automatic carpentry tools, jointers have the following advantages:
- It is possible to cut both large and small bars on them;
- They have a high quality cut;
- Possess the ability to process the edges and surfaces of wooden parts in curvilinear directions;
- If you equip the equipment with additional nozzles, then it can be used for sawing bars;
- They have a current price (starts from 10-14 thousand rubles).
Jointers are usually used in the woodworking segment of the industry, as well as in construction and carpentry. Small models can also be found in home workshops.
The main differences from the planer machine
Both of these devices are used for processing parts made of wood and other soft materials. The main differences between them are as follows:
- Reismus used for final processing of parts;
- The quality of the cut when working with a thickness gauge will depend on the technical capabilities of the machine, and when working on a jointer, on the skill of the operator;
- The thickness gauge, unlike the jointer, does not need an additional parallel side stop to process all four sides of the bar;
- To work on planer equipment, it is necessary to adjust the cutting depth of the knives into the surface to be machined.
In industrial production, planers and planers are used together: the latter sets the geometry of future products, and the former calibrates the machined part in terms of thickness.
Existing types of jointers
In total, there are two main types of jointers:
- Manual planer - this equipment is most often used in home workshops, it is distinguished by its low price and simplicity of design;
- Automatic (electric) jointer - it is characterized by a larger mass and increased power consumption. Its main advantages are increased productivity and high cutting accuracy, however, it costs a lot.
Also, planing devices can be classified according to the scope of application:
- Planing and planing - they perform only the function of planing;
- Planer-thickness planers - both planing and calibration are possible on them;
- Planer-circular - used for transverse / longitudinal sawing of bars and milling of blanks;
- Multifunctional (universal) - jointing, sawing, and sizing of boards, as well as drilling and grooving work are performed on them.
In home workshops, portable mini planers are usually used. They are easy to transport due to their low weight, but have reduced functional and performance properties.
Stationary machines are considered professional, which are divided into:
- Single-sided - they are equipped with a single working shaft and in one pass process only the lower part of the part. They do not have an automatic feed system for bars. Work productivity (i.e. planing speed) does not exceed 10 meters per minute;
- Double-sided - they have several planing shafts, which is why they can process all planes of the product at the same time, which specifically increases productivity. They have an automatic workpiece feeding system, which means increased work safety for the operator.
Features of the choice of jointers
In order to choose the right planer for yourself, you should be guided by the following criteria:
- The material for the manufacture of the desktop is usually silumin, aluminum alloys or cast iron. The latter is considered the most durable, but silumin countertops can be easily deformed during operation, which is why they are cheaper than the others.
- The dimensions of the working space (table) - this indicator must be chosen based on what size workpieces will have to be processed most often. For domestic needs, a table with a width of up to 15 cm and a length of no more than 140 cm is suitable.Industrial sizes are considered to be width up to 63 cm and length up to 2 meters - these are purchased for large woodworking shops.
- The number of knives - the more of them are fixed on the cutterhead, the less often they need to be sharpened. If it is not intended to intensively load the device, then 2 knives will be enough. For daily work, it is better to choose a model with 4 knives.
- Motor power and type - as a standard, planers are equipped with an asynchronous or commutator electric motor. They differ in design features and capacities. Collector power units are suitable for home models, but they are characterized by excessive noise. Asynchronous give the highest performance, but require large areas for placement.
- The revolutions of the knife shaft and the frequency of their rotation - the higher this indicator, the more accurately the cut occurs. The average figures for this criterion are 4.7 - 5 thousand revolutions per minute.
It is also worth paying attention to the brand of the manufacturer - professional and high-quality tools are made in Western Europe.
Planer knives
In their selection and application, it is necessary to rely on the following factors:
- The material from which the used knives are made depends on the type of wood being processed. For example, for processing pine bars or parts from other coniferous trees, you need to use knives made of P6M5 alloy. For softer rocks, HSS blades are perfect.
- If the main emphasis during work is on artistic carpentry, then straight and curly knives will become a necessity. With their high cutting accuracy, they will be able to create unique patterns and contours on the workpiece plane.
Due to the long period of use, knives are naturally subject to wear and require sharpening. The following signs will indicate the onset of this moment:
- During the operation of the machine, the electric motor becomes very hot;
- At the end of processing, the surface of the part does not take on a flat look, but on the contrary, there is some kind of “mossy”;
- The treated surface turned out with pronounced irregularities.
IMPORTANT! There always comes a moment when the old blades are simply impossible to sharpen due to purely physical features. In this case, it is better not to risk the safety of work, but to put in completely new knives.
Installing knives on a jointer
When attaching knives to the cutterhead, it is necessary to be guided by some features:
- After placing the knives in the grooves, you need to fix them tightly;
- Only with a clamp above the cutterhead is it possible to press the templates tightly against the edges of the worktable;
- The blade must be raised until it contacts the workpiece. In the place where they touch, a special mark is required;
- While fixing the bolts, the blades must be held tight;
- Upon completion of setting the first knife, the shaft must be rotated and continue setting the rest;
- After installation, you need to remove the template and change the angle of the bevel along the edge, as well as change the protrusion along the edge of the steel plates and cutterhead. Further, it is recommended to test the blades with the electric motor turned on.
IMPORTANT! The knives are fastened to the shaft only with wrenches (but not manually), in order to avoid the possibility of their loose fixation!
Hardware setup
This process should begin with checking the quality of sharpening knives - their blades should have an extreme bevel of 40 degrees, and the radius of the rounding edge should not exceed 8 millimeters.
After checking the sharpening, the knives must be fixed on the cutterhead. Before that, you need to lower the back and front tiles. During the installation of the cutting elements, it is necessary to check the parallelism of the blades - this factor should not be more than 0.1 mm per meter. To facilitate the adjustment, you can use a special indicator device.
Upon completion of the installation of knives, you need to check:
- The protrusion beyond the edge of the lining should not be more than 2 mm;
- The protrusion beyond the edge of the cutterhead must not exceed 22 mm.
Then you need to set the height of the desktop. The distance between the lips of the tiles and the cutting edge must be within 3mm, otherwise unplanned depressions may form on the workpiece during work.
The next step is to locate the guide. The distance between the left edge and the cutterhead ruler must always be greater than the width of the block of wood. The guide is determined by the template and fixed with screws.
The final stage will be a performance test by means of a trial run of the machine. The launch should not be accompanied by any malfunctions or visual deviations from the norm, and then work processes can continue on it. Otherwise, the setting should be repeated and, if problems are found again, repair or replace the defective parts.
A few basic jointing rules
In the process of working with wooden blanks on the machine, a number of simple rules must be observed:
- The jointer must be held with both hands: the right one is located on the block, and the left one is on the control handle;
- When planing, the device must be guided along the wood fibers, and the device can be pushed by its own muscular strength;
- To process the edge, it is necessary to turn the beam with the required side to the knives and trim it in the order described above.
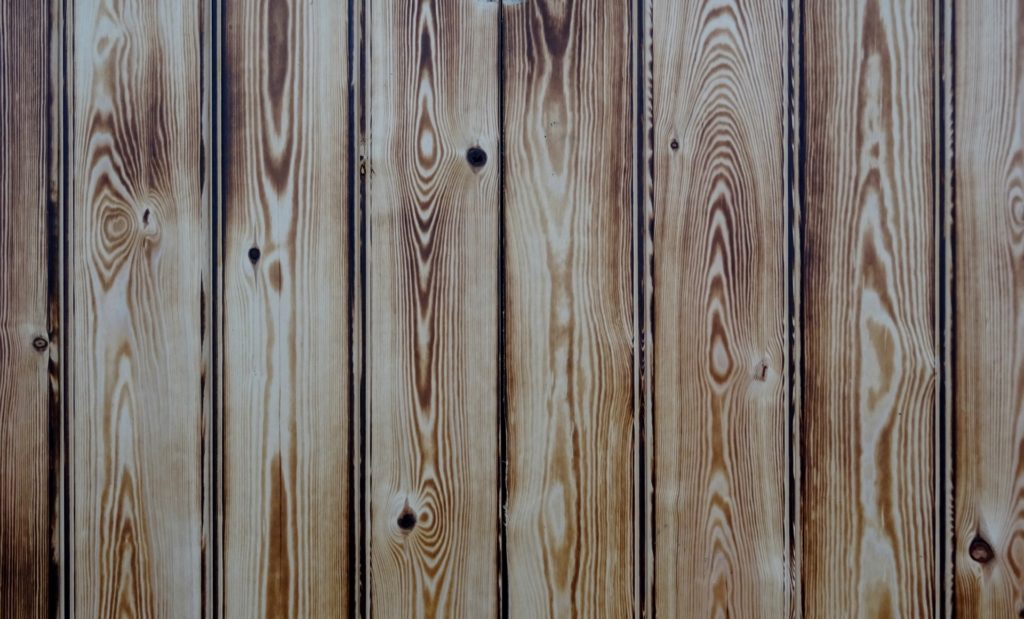
Safety basics
- It is forbidden to touch the blades when the machine engine is on;
- All work is carried out only in overalls: a protective headgear should be on the head, hands should be in gloves, eyes should be protected with special glasses (it is important that all elements of personal protective equipment fit snugly against the body);
- In the process of jointing, in order not to damage the fingers with knives, it is necessary to use clamping holders;
- For more precise processing and in order to prevent cutting off excess layers from the part, a special marking line is applied to its surface using chalk. If after processing it disappeared completely, then the surface can be considered smooth.
Popular manufacturers and cost
Modern companies offer many samples of the equipment in question, differing in their configuration, price and quality. However, even with rather modest financial capabilities, it is possible to pick up and purchase a decent machine for work purposes. And even foreign manufacturers in this regard offer affordable prices. These include the firms "Stomana" and "GriGGIO". At the same time, domestic manufacturers will also be able to provide tools that have excellent performance in terms of the price / quality ratio. Among these, one can note the products of the Kuibyshev Machine Tool Plant.
The cost of professional models for the industry is very high. The price here will primarily depend on the configuration, and then on the manufacturer.A standard industrial machine will cost about 150,000 - 200,000 rubles. Home equipment is much cheaper, but it is less functional. The price of household tools ranges from 15,000 to 20,000 rubles. At the same time, according to user reviews, the first place in the Russian Federation today in terms of functionality and performance is occupied by the SF-400A model from KSZ JSC - the machine is considered semi-professional and costs about 100,000 rubles.
Rating of the best jointers for 2025
Budget class (household models)
3rd place: Encore Corvette 24
This model has a lot of functions for a home machine: it can perform rough planing, jointing of various sizes and even sizing lumber. The machine has an automatic workpiece feeding system, and it is also equipped with a thermal motor protection and a magnetic start device.
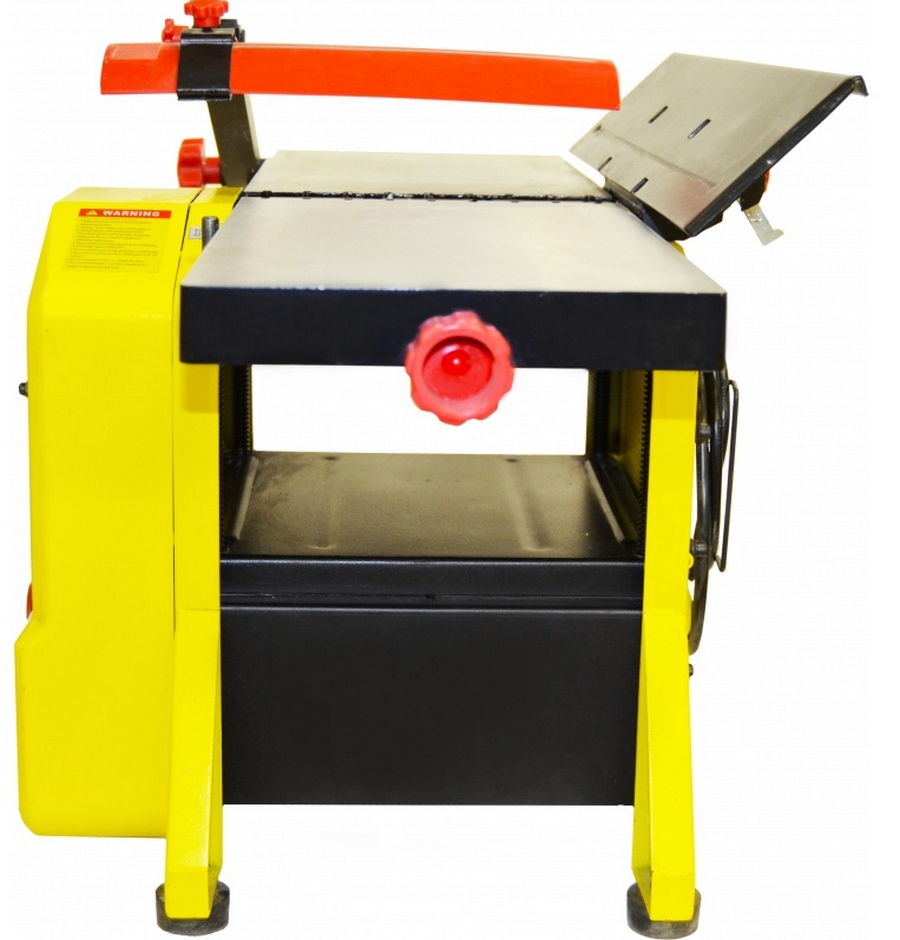
Encore Corvette 24
Advantages:
- Versatility;
- Availability of additional options;
- Economic cost.
Flaws:
2nd place: Special SRM-2000
Due to its cast base, the design of this model is particularly rigid. This will have a positive effect on the sizing of the timber and the unedged/edged board. The model is equipped with a high-power collector motor. There is an automatic protection against power overloads. Additionally, a belt drive is installed, providing some degree of noise reduction.
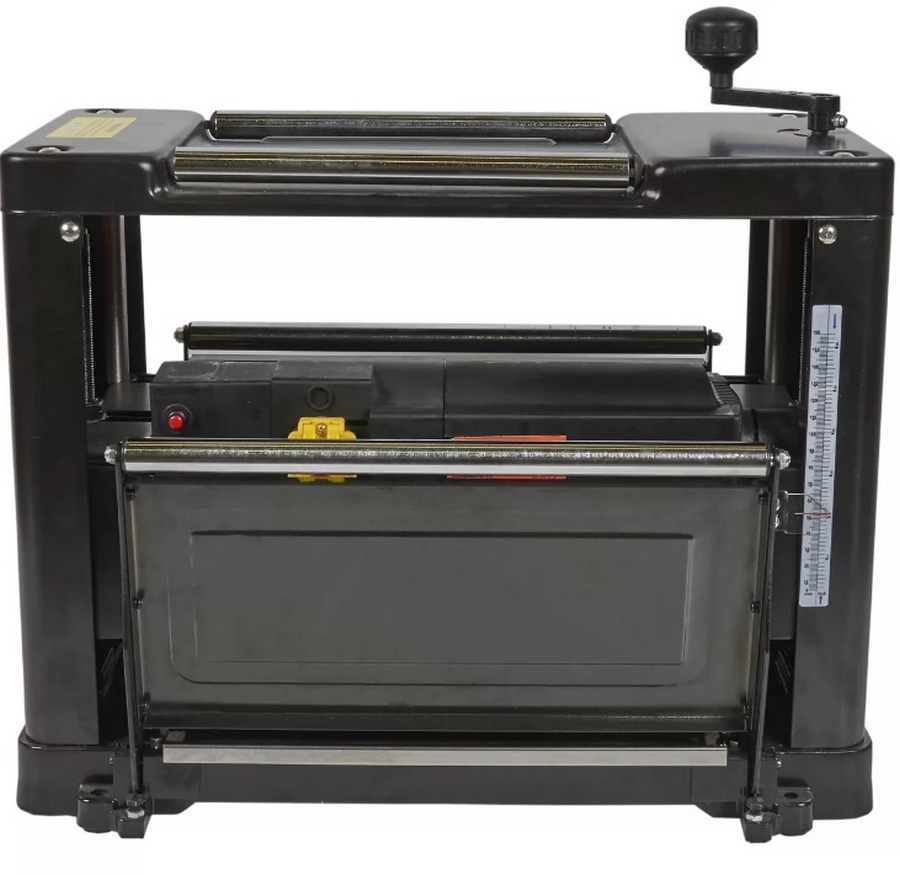
Name | Index |
power, kWt | 2 |
Shaft rotation, rpm | 8000 |
Planing depth, mm | 3 |
Weight, kg | 40 |
Price, rubles | 21000 |
Special SRM-2000
Advantages:
- Possibility of simplified interaction with long objects;
- The height of the workpiece is increased to 160 mm;
- Auxiliary rollers for the guide are supplied with the kit.
Flaws:
- Difficulties in transportation (monolithic base).
1st place: Interskol RS 330
High-quality processing of materials on this machine is achieved through the use of increased shaft speeds, equipped with two blades. At the same time, the tool is characterized by reduced noise, despite the use of a chain drive in the design. There is a chip removal from the desktop, a special nozzle for a vacuum cleaner is included.
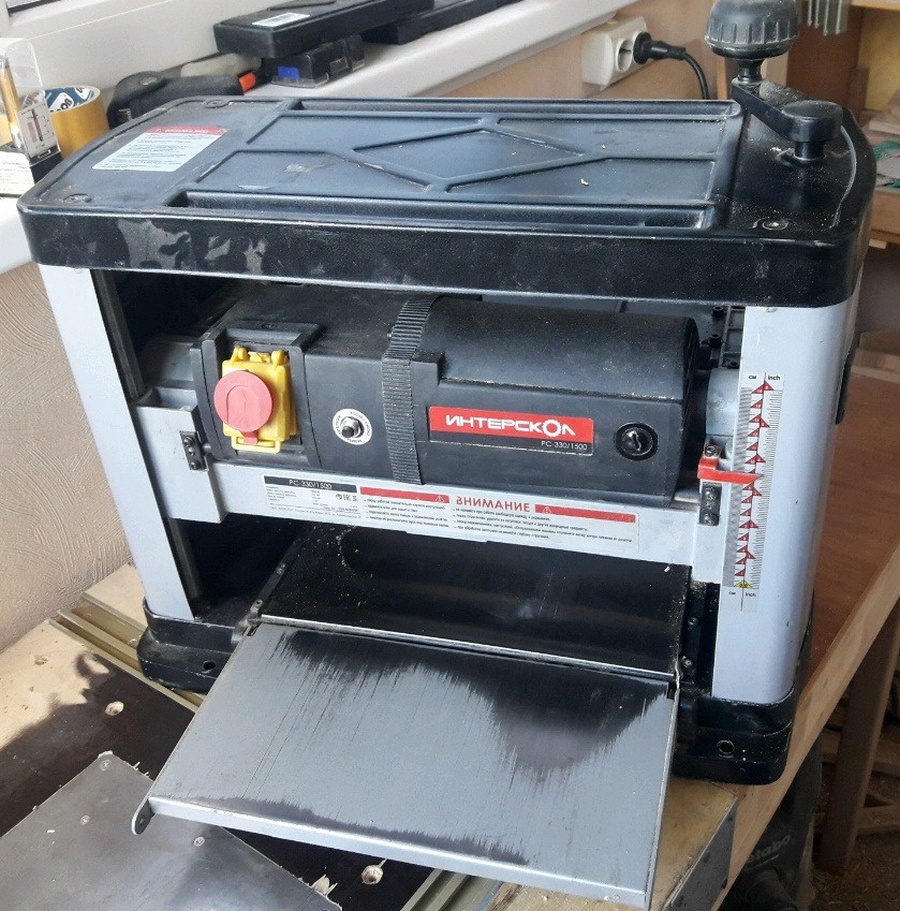
Name | Index |
power, kWt | 1.5 |
Shaft rotation, rpm | 9000 |
Planing depth, mm | 2.8 |
Weight, kg | 35 |
Price, rubles | 26000 |
Interskol RS 330
Advantages:
- Implemented additional security measures (protection of moving parts);
- Great working potential;
- Equipped with automatic pull.
Flaws:
- It is forbidden to process workpieces with a high level of humidity.
Middle segment (semi-professional)
3rd place: JET JWP 12
A good example of semi-professional equipment. Favorably differs with sufficient power of the collector motor, good autofeed speed and increased speed of the cutter shaft. Work tables are made folding for ease of transportation. A block thermal relay is implemented in the design.
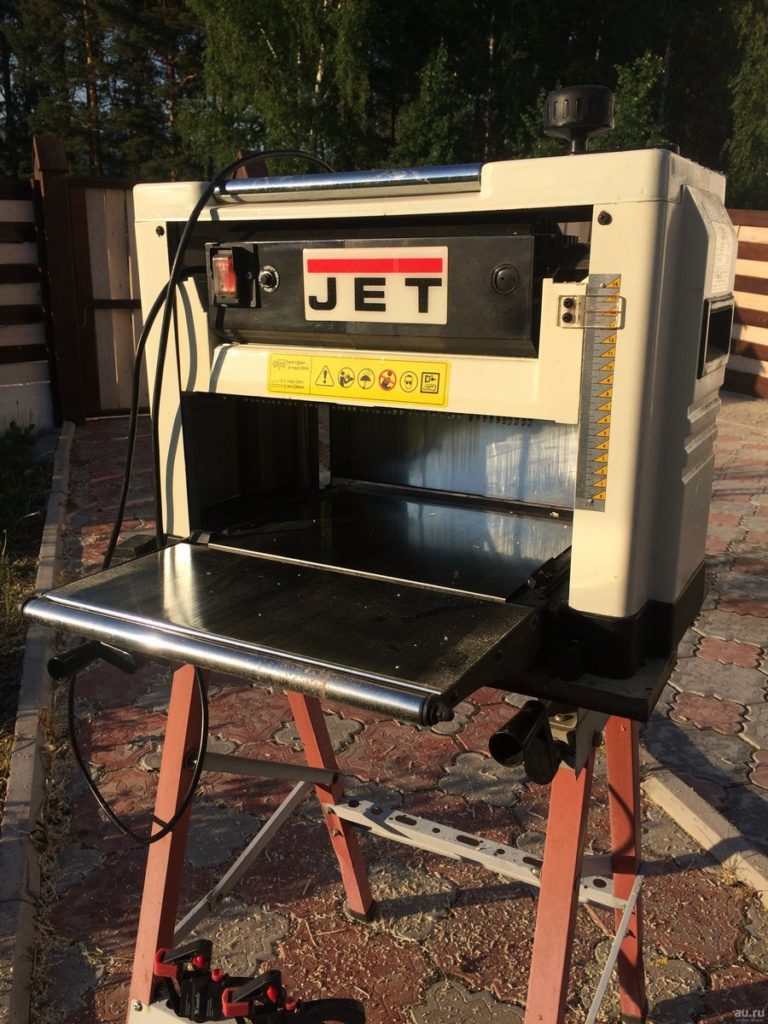
Name | Index |
power, kWt | 1.8 |
Shaft rotation, rpm | 9000 |
Planing depth, mm | 2.5 |
Weight, kg | 27 |
Price, rubles | 29000 |
JET JWP 12
Advantages:
- Has an emergency key (instant forced shutdown);
- There is protection against overheating;
- High-speed cutting shaft.
Flaws:
- Requires constant self-removal of chips.
2nd place: JET JPT 10b
The machine is an excellent example of equipment from the middle price category. It is characterized by sufficient versatility. It is additionally equipped with an engine temperature control system. There is a special stop for the jointer and a sensitive planing depth regulator.
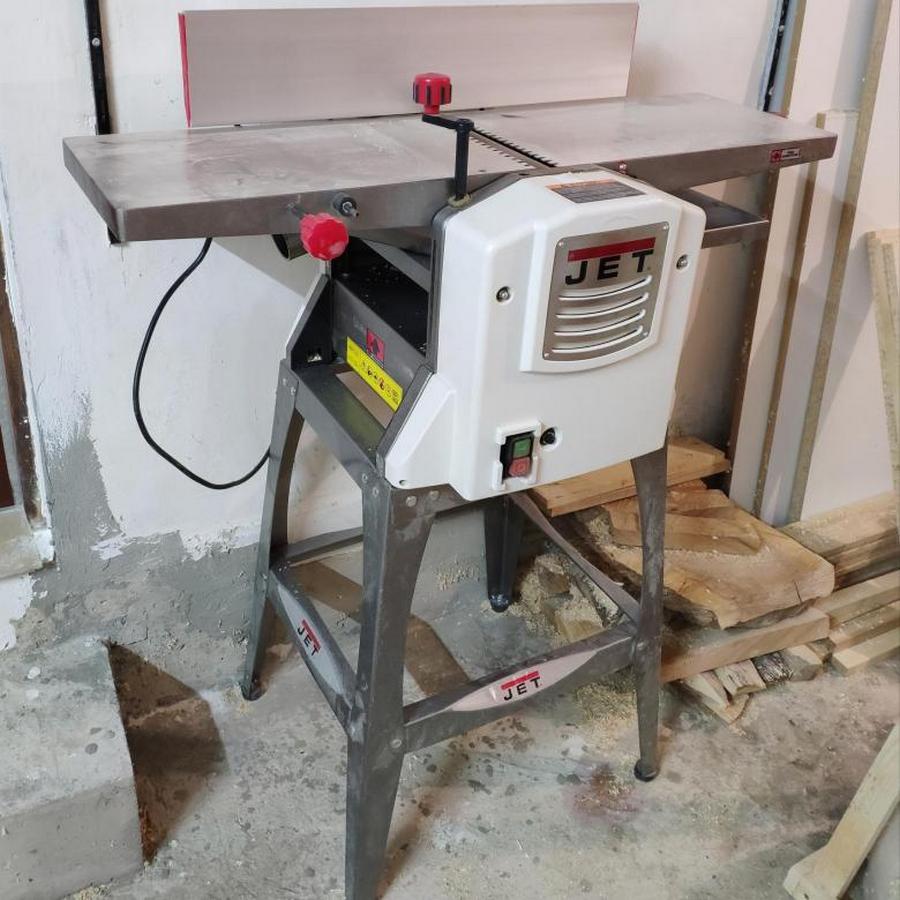
Name | Index |
power, kWt | 1.5 |
Shaft rotation, rpm | 9000 |
Planing depth, mm | 3 |
Weight, kg | 34 |
Price, rubles | 32000 |
JET JPT 10b
Advantages:
- Additional options;
- Multifunctional adjustment;
- Current price.
Flaws:
1st place: Hitachi P13f
The machine has a very sensitive planing depth adjustment system, which proves that it belongs more to professional equipment. With proper setup and suitable dimensions of the board, the operator’s task will only be to control and then receive the finished part. It has a start button protected by a lid.
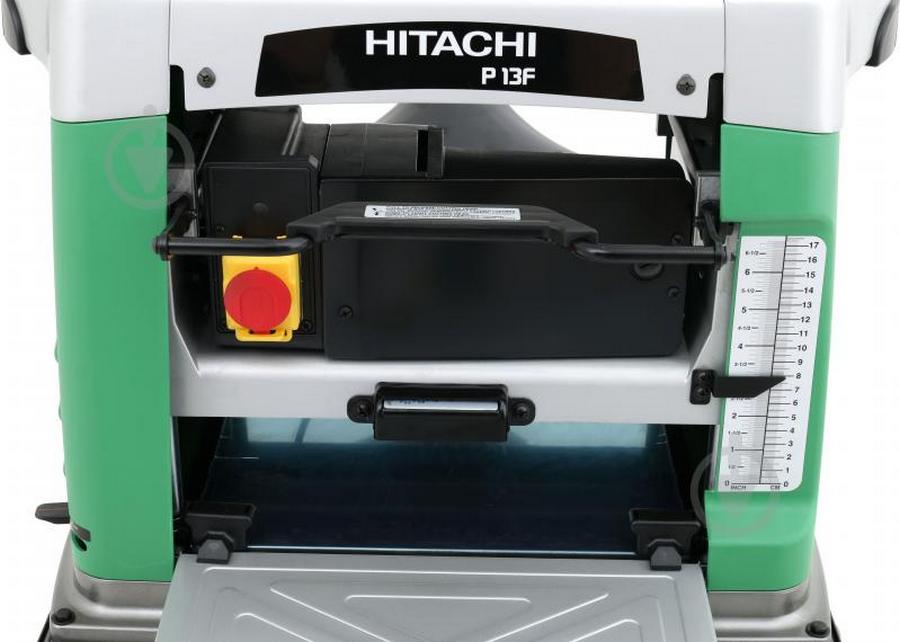
Name | Index |
power, kWt | 1.8 |
Shaft rotation, rpm | 9300 |
Planing depth, mm | 2.4 |
Weight, kg | 46 |
Price, rubles | 36000 |
Hitachi R13f
Advantages:
- Most processes are automated;
- Improved security features;
- Good cutting depth.
Flaws:
Premium class (professional)
3rd place: Makita 2012 NB
This tool has a reduced backlash, which provides increased comfort during operations. And this is achieved through the use of compression springs and bearings at the base of the bolts. The double insulation does not require the machine to be grounded, and the factory-set depth adjustment is extremely accurate. Of the minuses - after transportation, re-adjustment of the guides is required.
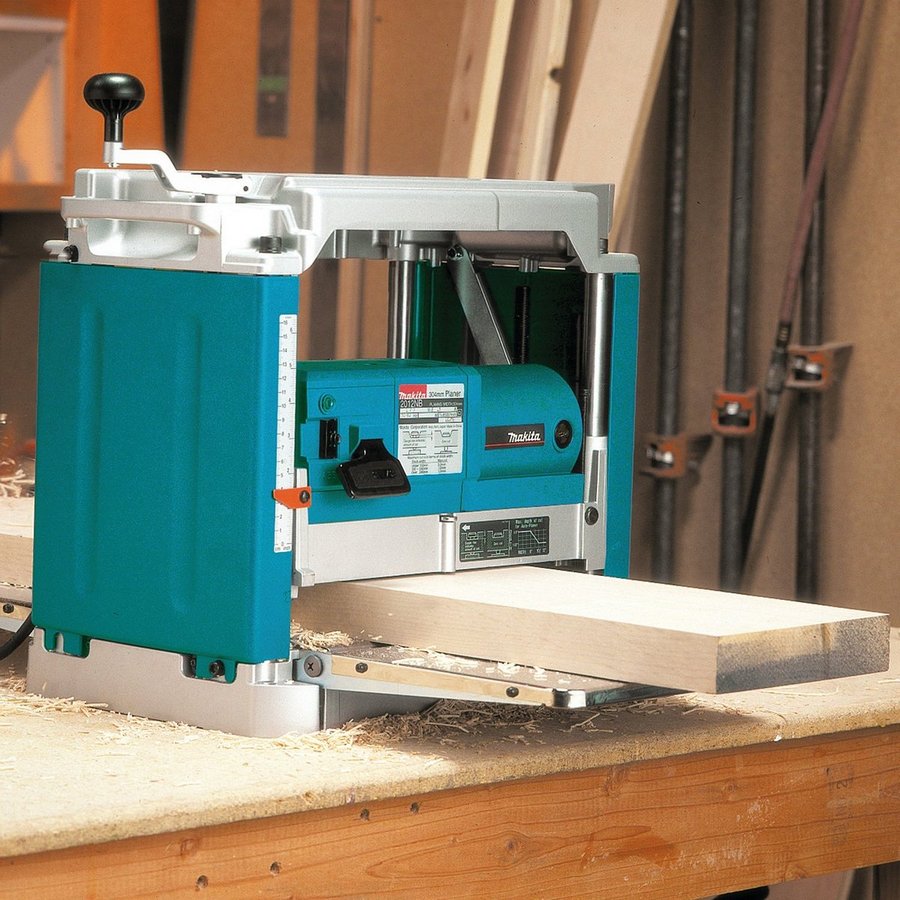
Name | Index |
power, kWt | 1.65 |
Shaft rotation, rpm | 8500 |
Planing depth, mm | 3 |
Weight, kg | 27 |
Price, rubles | 41000 |
Makita 2012 NB
Advantages:
- Low weight;
- Additional templates;
- Removable pencil case.
Flaws:
- Need to readjust after shipping.
2nd place: DeWalt 733
A special tool developed across the Atlantic for sale on the foreign market. Strict blocking of the planing element is implemented in case of insurmountable obstacles (knife blades last longer). Rulers and measuring parts are designed for the metric system. The machine is equipped with a reinforced frame, a cast bed, tables are fixed especially securely.
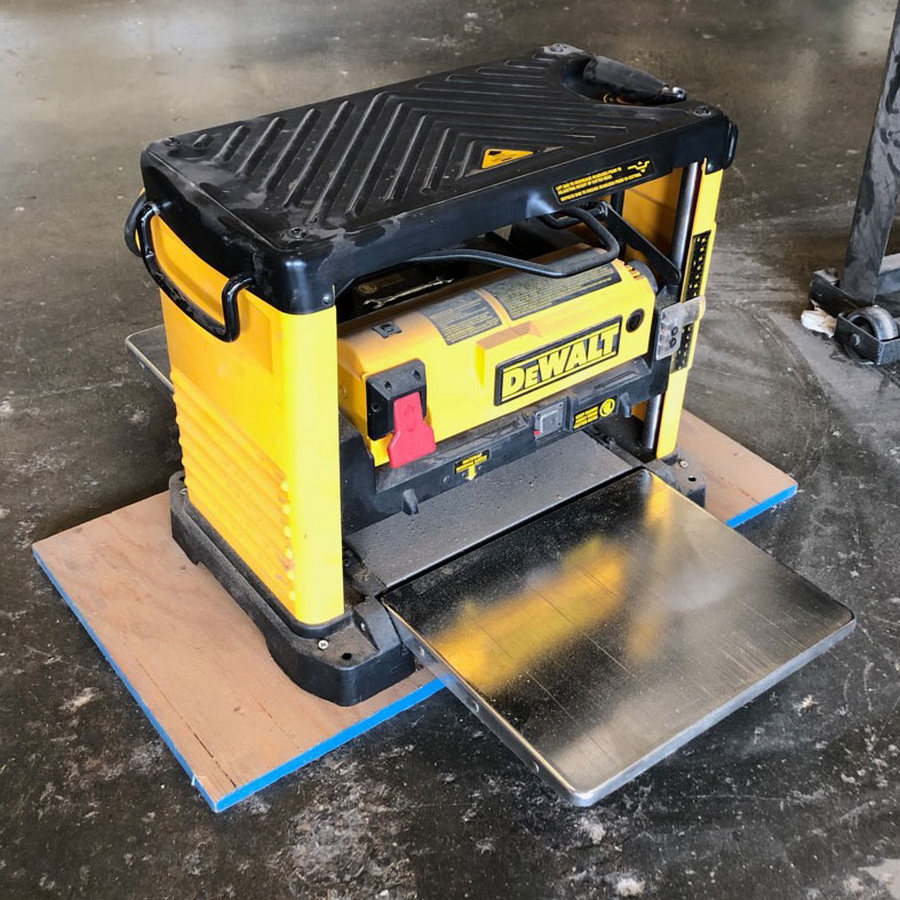
Name | Index |
power, kWt | 1.8 |
Shaft rotation, rpm | 10000 |
Planing depth, mm | 2 |
Weight, kg | 33 |
Price, rubles | 53000 |
DeWalt 733
Advantages:
- Fixation of the planing shaft;
- Reinforced frame and bed;
- High shaft speed.
Flaws:
1st place: Metabo HC 260
The tool originally combines small dimensions with a large weight, a powerful engine with a low shaft speed. However, it has a cast iron table with an adjustable stop, which indicates its potential for heavy use. According to customer reviews, it may well perform the most complex operations on an industrial scale.
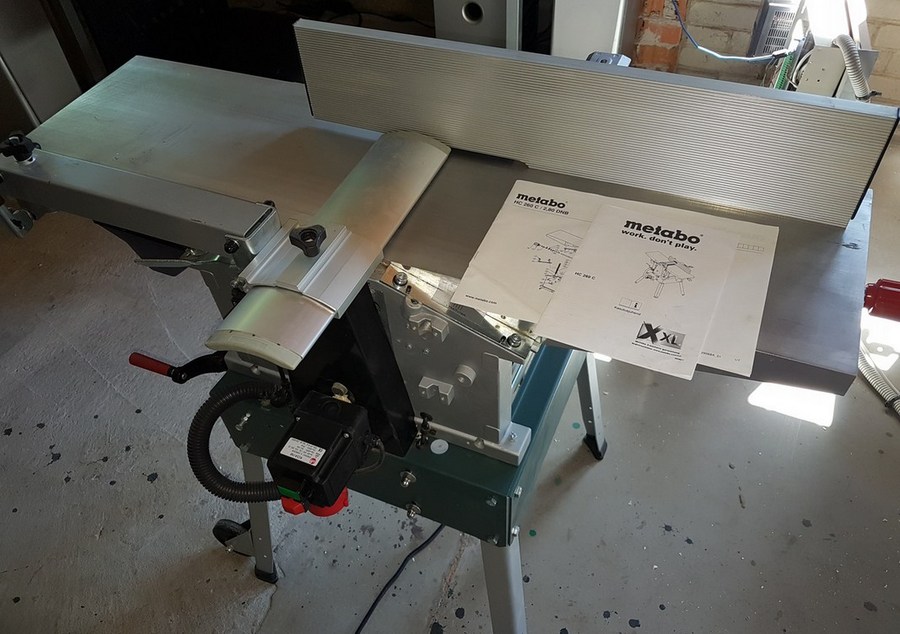
Name | Index |
power, kWt | 2.2 |
Shaft rotation, rpm | 6500 |
Planing depth, mm | 3 |
Weight, kg | 71 |
Price, rubles | 74000 |
Metabo HC 260
Advantages:
- Blocking the board in the event of a "reverse strike";
- Magnetic switch;
- Versatility.
Flaws:
Instead of an epilogue
The tools discussed in this article are complex technical equipment, so it is more expedient to purchase them from authorized dealers.The purchase of such a product "from hand" means the absence of any warranty obligations on the part of the seller. If you buy through online sites, then you should do it only on trusted sites. Buying at retail from an authorized dealer can be somewhat more expensive, but often they are also authorized service centers for repairs.