Building a dwelling according to the classic brick "technology" is a laborious and lengthy process. And this not only depends on the general uncertainty of the deadlines for completion, but also almost always involves additional costs like changing contractors, etc. An alternative to all this "long-playing" action can be the use of prefabricated houses technology. The cost of these buildings can be calculated quite accurately even at the stage of ordering components and building materials. At such construction, the contractor simply does not have time to change, because the construction period does not exceed two months maximum. Interior decoration takes a minimum period, because the material of the walls is already sheathed with even sheets that do not require special plastering.The only obstacle can be only a fundamental issue of the very first stage - the choice of a suitable building technology.
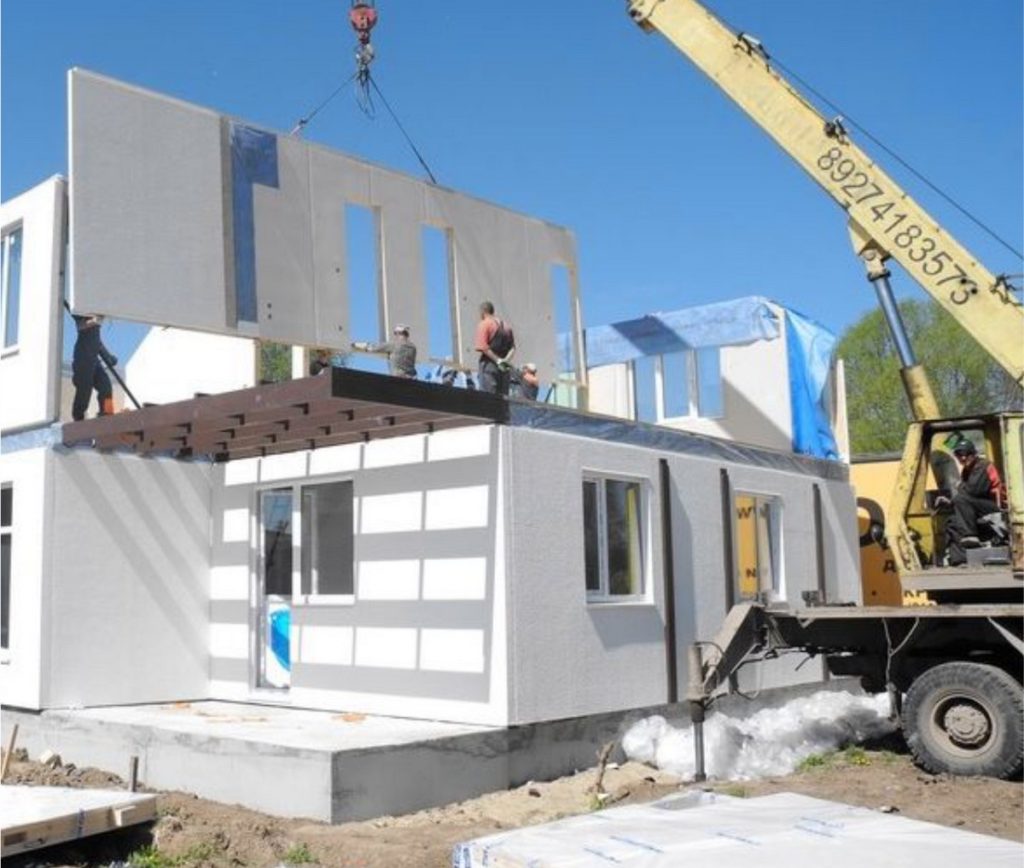
Technologies for accelerated construction of houses - general information
Nowadays, several basic prefabricated construction methods are used, which are named after the country of their invention / application and differ in their energy and environmental parameters. However, they have one general principle - the frame of the structure is always sheathed with insulation and lined with a lightweight finishing material. For each specific case, it will be necessary to take into account such indicators as the heat-conducting coefficient, the ability to pass vapors, and the norms for arranging a hinged facade.Any mistake can lead to a decrease in the life of the entire structure at times, so most of these calculations should be made exclusively by professionals. In total, three regional technologies can be distinguished:
- Canadian - it is distinguished by a special arrangement of the foundation and the setting of shields from which the house is assembled. During the construction, factory-made SIP-panels of the "sandwich" type are used, the connection of which is carried out by means of a beam. A house assembled from such panels has a large margin of safety due to the use of a pair of power systems on the frame and insulation - these are SIP panels and timber.
- German - it also involves assembly on the basis of ready-made panel panels, but which, upon final installation, are assembled into large house kits. Further, according to the plan, doors and windows are built into the building, electrical wiring is laid. The task of the builders is only to collect all the house kits together.
- Finnish - it provides for a frame-frame installation method that does not require the involvement of a large team of workers. For the frame, both a metal profile and a standard beam can be used. The entire structure is installed on a pile or slab foundation (it is allowed to use a shallow foundation foundation).
Advantages and disadvantages of "fast" houses
Houses assembled as a constructor in a short time have a number of undoubted advantages:
- Save time - the quick construction of the building can be carried out at any time of the year. You don't have to deal with leveling walls for interior decoration, as they already come with the right degree of evenness.
- Affordable prices - in addition to the affordable price for a constructor building, one should take into account savings on construction work and materials, as well as related costs (from workers' salaries to payment for construction site security services).
- Energy Efficiency - A prefabricated building is unlikely to generate costs of more than 40 kWh per square meter during the heating season. This figure is two times less than that of a classic house with the same area. Thus, there is additional savings on electricity and heating.
If we talk about the minuses, then there are almost none (for the budget price segment). Of course, the main disadvantage will be the durability factor, because it will not be possible to build a family nest from a designer house that can last a dozen centuries, but it is quite possible to count on two generations of a family. Also, it is worth mentioning that the types of buildings in question cannot have more than two floors.
Types of prefabricated houses
Foam and aerated concrete
The term of their construction is no more than 60 days. They are considered more reliable and durable than houses made of other "fast" materials, while they have the proper level of internal comfort. Their advantages include:
- Excellent heat retention:
- Easy processing and cutting of blocks;
- Gas and foam concrete "breathe" well;
- The problem of hammering nails does not arise (metal is perfectly included in such a base).
Among the shortcomings, one can name excessive accumulation of moisture (it will be necessary to treat the walls with protection from atmospheric precipitation) and low strength (if we compare them with capital buildings made of real concrete and brick).
Panel and panel-frame
Their construction period is about 1.5 months.The resulting building will not be subject to excessive shrinkage, will show excellent thermal insulation qualities, repairs will be possible at any time of the year. Among their advantages it is possible to mention:
- No shrinkage;
- Shields and panels immediately have all the necessary tie-ins and installations;
- A powerful foundation is not required - you can be content with lightweight.
Unfortunately, this type of structure has several key "cons":
- Differs in poor sound insulation and ventilation;
- Nails are poorly perceived (driven in) by walls;
- External insulation can withstand no more than 30 years;
- Possesses poor resistance to adverse natural and meteorological phenomena (for example, earthquakes and hurricanes).
Modular
They are built in 2-5 weeks and use "German" technology. All elements are prefabricated and delivered to the construction site ready-made, where they are connected on a prepared foundation. The construction period may include terms for individually manufacturing all modules and equipping them with communications and appropriate openings (windows and doors). Benefits can be listed:
- Ability to assemble regardless of the season;
- Increased strength;
- Resistant to difficult operating conditions.
Of the shortcomings worth mentioning:
- The need to equip the future construction site with entrances for special equipment, which will bring large and equipped modules;
- Somewhat inflated prices;
- The focus is more on individual orders (standard types of modules are almost never practiced and are not produced).
Wooden log cabins
This type is a long-term construction (by the standards of prefabricated houses) and is built within 6-7 weeks.Its characteristic feature is its excellent energy saving performance. Additional typical features include:
- Resistance to temperature extremes;
- The log structure allows the whole house to "breathe";
- Excellent air filtration;
- Does not require a reinforced foundation.
The disadvantages include:
- Low fire safety - the design will definitely require treatment with fire-fighting impregnations;
- Shrinkage occurs within 3 years;
- Regular preventive treatment of the timber will be required in order to prevent rotting and the spread of harmful insects.
Thermohouses
They are built on the basis of polystyrene blocks, which are poured with concrete. Their erection can take up to 8 weeks. These structures are characterized by high heating costs, however, the structure itself is easy to install, so it will not require the cost of attracting professional workers. The advantages of a thermal home include:
- Ease of assembly;
- No need to level the walls;
- Good performance in terms of sound insulation;
- Sufficient environmental safety;
- Variability of architectural construction and layouts;
- Democratic building rates.
Among the shortcomings it is possible to name:
- Increased vapor permeability, which can create a high level of humidity inside, which means that it is mandatory to install a supply and exhaust ventilation system;
- Fragility (10-15 full years of operation without repair);
- Susceptibility to the destruction of building materials during permanent operation at low temperatures;
- The material is not recommended for the construction of medical and children's facilities.
Problems of choosing a foundation for prefabricated houses
Not every prefabricated building can do with a lightweight version of the foundation. Naturally, if it is planned to build a house from a bar, then you can use a lightweight version of the base, even if the plan provides for 2 floors. But such a structure will not allow the placement of massive furniture or other weighty objects inside, which will very quickly lead the entire structure, if not to immediate shrinkage, then to a mandatory roll. From this it is clear that even for simple building options it is much more reliable to use a powerful foundation. Also, there are several conditions under which a reinforced base will simply be necessary:
- Construction in difficult places - here we mean construction on the banks and cliffs of water bodies (both standing and flowing). Before performing the foundation in such conditions, one should take care of the issue of a seasonal increase in the level of water (both external and ground), but professionals recommend arranging a pile foundation for such situations.
- The presence of clay soils - in places with this type of soil, a reinforced base is a must. Bases with a depth of 60 centimeters of a monolithic type, preferably a tape structure, are perfect.
- Presence of freezing soils - if soils are expected to freeze quickly in winter, and when the moisture present in them freezes, they will be subject to physical expansion. Thus, while these processes are taking place, the house structure will involuntarily move and stagger, which will subsequently cause cracks and distortions of the structure. Laying the foundation below the freezing zone will help to avoid such problems.
- The presence of fine sandy soils - such soil is also not very stable, although it slightly absorbs moisture. It is more susceptible to flow properties that affect the stability of the house, which will affect its uneven shrinkage. It is possible to minimize the negative consequences by adding gravel and sand before arranging the base (it is allowed to use the ASG mixture, provided that it is subsequently properly compacted).
Characteristic features of prefabricated houses
In modern Western countries, more than 70% of the individual housing stock is built according to the technology under consideration. So foreigners are trying to fight for the environment, for the restoration of forests, and also make attempts to create comfort and isolation of housing for each citizen. This trend is especially clearly seen in the example of the northern territories: Canada, Scandinavia, Alaska, Greenland, Iceland, etc. Residents of these regions positively evaluate such buildings that can provide the necessary comfort, while retaining heat no worse than ordinary wooden buildings or city apartments. Moreover, in such structures there are no heavy floors, and the foundation base does not have to be monolithic and high. Also, popularity is explained by affordable price and fast construction time.
Prices for prefabricated houses
In the vastness of our Motherland, potential homeowners estimate the average cost of one square meter in the type of dwelling under consideration (excluding the cost of utilities, external elements and land) at 17,500 rubles per sq.m.
However, some modular structures may have a slightly higher price tag due to their designer finishes.As a result, the construction of a "fast house" on 70 square meters of space can cost from 700 thousand to 5 million rubles (depending on internal and external features). It is also possible to build a very large version with several floors and an area of up to 800 square meters, which can cost around 35 million rubles.
If we analyze the average tariffs for prefabricated housing, which is constructed on a turnkey basis, based on SIP technologies, frame-panel, prefabricated or modular, then they will always be cheaper than similar buildings made by traditional methods. There are two main reasons for this:
- Reduction of production waste - in traditional construction, as a rule, several contractors work, each of which is responsible for its own area of work and which leaves behind garbage. When assembling a “quick home”, the contractor, in most cases, is the only one, respectively, and there is less waste from him.
- Low labor and time costs - in traditional work, each group of contractors begins its activities only after the other group has prepared all the conditions for this. For example, until the common frame of the building is erected by some workers, the laying of engineering communications by another group will be impossible. At the "quick house" everything comes immediately in the kit and does not involve long time gaps in the order of work.
If we talk about the high cost of interior decoration, then for the type of construction under consideration it will not become too expensive, because for the most part it has already been done before assembly. For the traditional construction of houses, this process is stretched and includes the selection, purchase and finishing of premises with materials, which can be carried out even by more than one or two contractors.Speaking about the specific figures of this issue, it can be noted with confidence that the customer can save at least 20% of their usual price on work and finishing materials.
Rating of the best prefabricated houses for 2022
House kits
Modular houses HOMEFORT
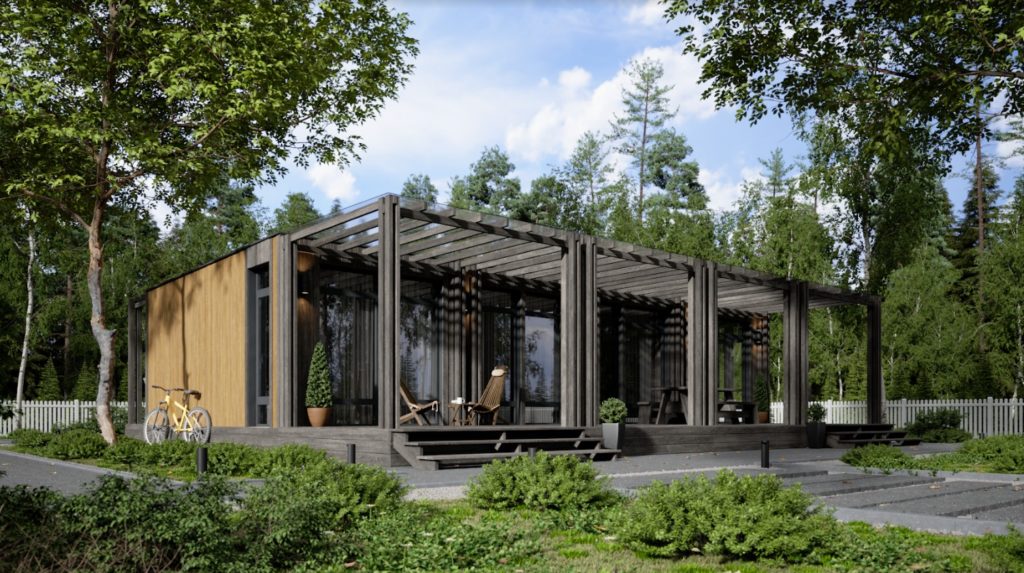
HOMEFORT modular houses have been sold on the Russian market since 2021. Before that, the company produced frame structures. There are 4 modifications of houses in the catalog of the company, which include 1-room buildings with an entrance hall, a plumbing unit, a terrace and a porch (the total area of this model is 28 sq. M), as well as 4-block three-room houses with a kitchen-living room, a plumbing unit, entrance hall, terrace and porch (the total area of this modification is 98 sq. m.). The ceiling height is 2.7 meters.
The manufacturer writes about the excellent energy efficiency of its models due to the applied heat-insulating mineral wool boards manufactured by Knauf, as well as the installation of double-glazed windows with i-coating. In addition, the technology for building frame-type houses is one of the best in terms of cost when it comes to energy efficiency.
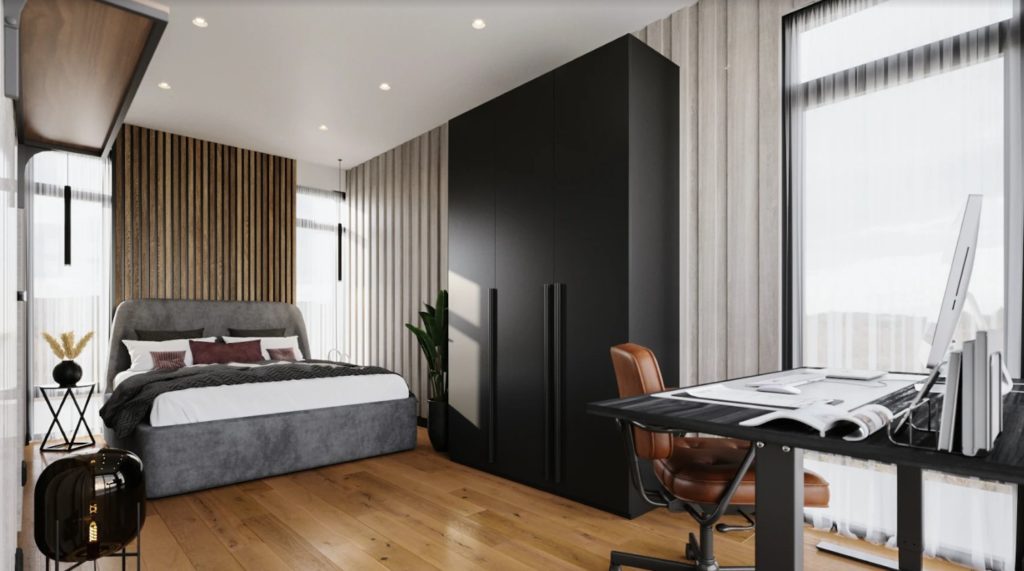
Additionally, the base price includes an air recovery system that provides a constant flow of fresh air from the outside, while maintaining a comfortable temperature inside the house. Finishing, delivery of the structure, foundation and connection of communications are included in the price.
The term of production assembly is from 3 months. The materials used in the manufacture have the required certificates. The manufacturer offers 2 finishes - in dark and light colors. In addition, in these designs, the specialists thought out 4 planning options (selected at the request of the client).If the owner decides to move, the house can be transported and put in a new location.
Average price of goods: 1900000 rubles.
Advantages:
- The base price includes delivery, foundation, finishes and plumbing fixtures.
- Relative affordability.
- Designs differ from competitors in excellent energy efficiency.
- 2 finishes.
Flaws:
"LLC PKF "Sibstroy" option No. 2 "European"
A similar project was implemented only twice, it was made from standard house kits and is under technical supervision in the south-west of the Moscow region. The building consists of MEGABLOK polystyrene-concrete wall panels, has an urban design, typical of suburban real estate in Western Europe in the mid-2000s, and a layout for the everyday life of a small family. The compact plan contains everything you need for everyday life and relaxation: a spacious living room of 37 m2 with a kitchen, a living room (guest room), a pantry, a bathroom on the ground floor and three fairly spacious bedrooms with a bathroom of almost 9 m2 on the second floor. The basic configuration tariff is 984,000 rubles.
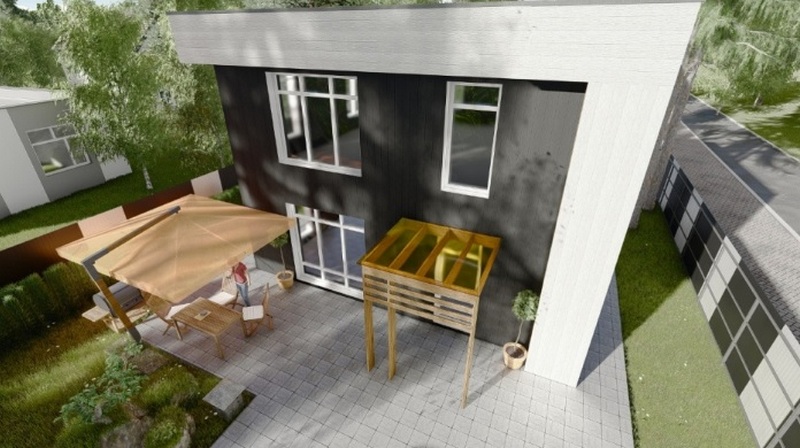
prefabricated house LLC PKF "Sibstroy" option No. 2 "European
Advantages:
- Total area of 141 square meters;
- 4 bedrooms;
- Possibility of technical supervision after construction.
Flaws:
- Few practical implementations.
"LLC PKF "Sibstroy" option No. 4 "Chalet"
This option takes into account the wishes for a small and inexpensive country house. Excellent adaptation of the material to the project, a gable roof for warm polystyrene concrete slabs, high-quality ceilings, allow assembly directly “from the wheels” in just a couple of weeks.The cottage, built from polystyrene concrete wall panels, has a conservative design and layout, typical for suburban real estate of the 20th century. The compact plan contains everything you need for everyday life and weekends: a living room of 24.5 m2 combined with a kitchen, a living room of 13.4 m2 (guest room), a bedroom of 13.9 m2, two bathrooms and all on the same floor. Basic configuration tariff - 638,000 rubles
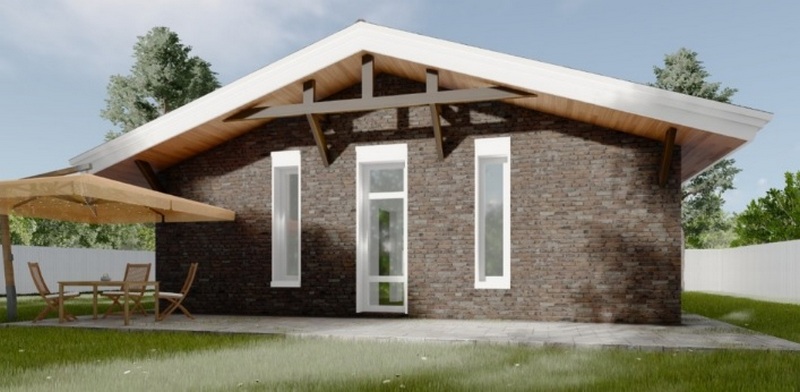
prefabricated house "LLC PKF "Sibstroy" option No. 4 "Chalet
Advantages:
- Sufficient footage;
- Conservative design;
- Democratic pricing.
Flaws:
"LLC PKF "Sibstroy" option No. 1 "Native"
This is the most popular suburban project from this manufacturer. During the work, more than 500 houses were built according to this plan, and therefore there is a well-established estimate and a clear understanding of the entire scope of work. Designed and built cottage of polystyrene concrete wall panels "MEGABLOK" has a classic design and well-thought-out layout. The experience of building country cottages ensures that upon completion of the work, the building will become warm, cozy and practical, and even more so not too burdensome for the budget. The basic configuration tariff is 906,000 rubles.
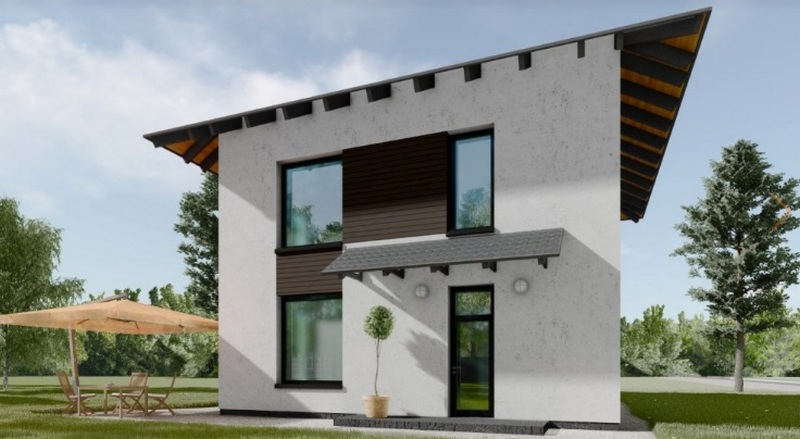
prefabricated house LLC PKF "Sibstroy" option No. 1 "Native
Advantages:
- Popular project;
- Use of innovative Megablock panels;
- Thoughtful layout.
Flaws:
"LLC PKF "Sibstroy" option No. 3 "European-2"
The new project No. 3 "European-2" of the Sibstroy company has experience in the implementation and construction of suburban real estate since 2007. The most frequent wishes of customers are also taken into account.Excellent adaptation of the material to the stated requirements and a flat roof allows you to work directly "from the wheels" in just 1-2 weeks. The building made of polystyrene concrete wall panels has a modern design, typical for suburban real estate in Eastern Europe in the early 2000s, as well as a layout for everyday family life. The compact layout accommodates everything you need for everyday life and weekends: a spacious living room of 34 m2 combined with a kitchen, a living room of 15 m2 (guest room), bathroom on the ground floor and three bedrooms, bathroom almost on the second floor. The tariff in the basic configuration is 971,000 rubles.
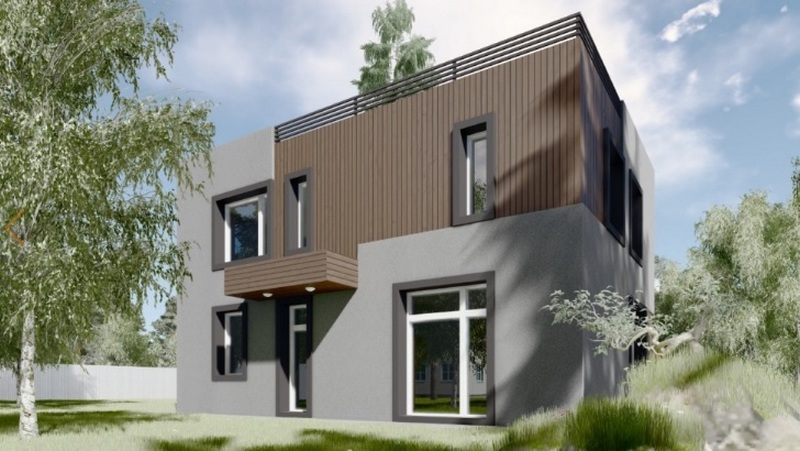
prefabricated house LLC PKF "Sibstroy" option No. 3 "European-2
Advantages:
- The latest project;
- The presence of many separate rooms;
- 2 floors on 130 square meters.
Flaws:
SIP-panel buildings
4th place: "LLC "Turnkey" option "ARKTUR"
The model has the following parameters: total area - 56 m2, living rooms - 3, total dimensions - 10x5 m. The design includes: a terrace, panoramic windows. This small house is perfect for arranging a modest suburban area, especially if the surrounding nature does not allow for large-scale construction (or it is generally prohibited). The project provides all the necessary minimum amenities for a small family. The cost in the basic configuration is 1,800,000 rubles.
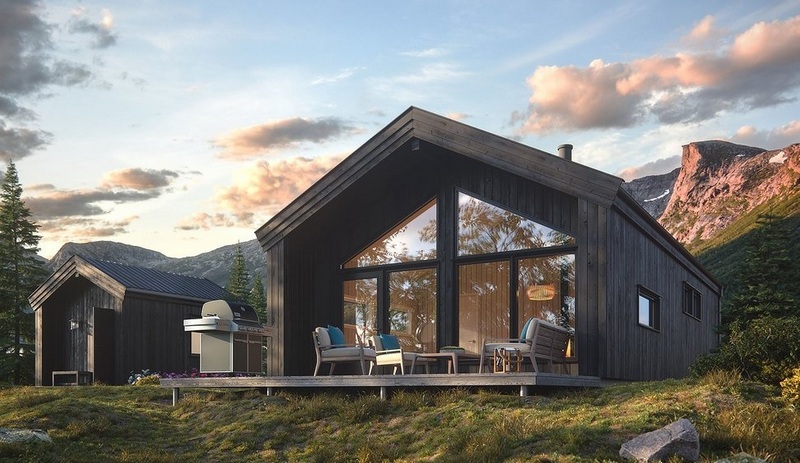
prefabricated house LLC "Pod klyuch" option "ARKTUR
Advantages:
- Suitable for small suburban areas;
- Very democratic price tag;
- The presence of an attached terrace.
Flaws:
- The minimum set of amenities.
3rd place: "LLC "Turnkey" option "Velya"
The building has the following characteristics: total area 146 m2, living rooms - 5, total dimensions 18x12 m. The structure includes: a house terrace and a sauna. The project is already a full-fledged country cottage with a large area, which can be used for permanent residence, regardless of the season. Implemented an additional option in the form of a sauna. The cost in the basic configuration is 4,130,000 rubles.
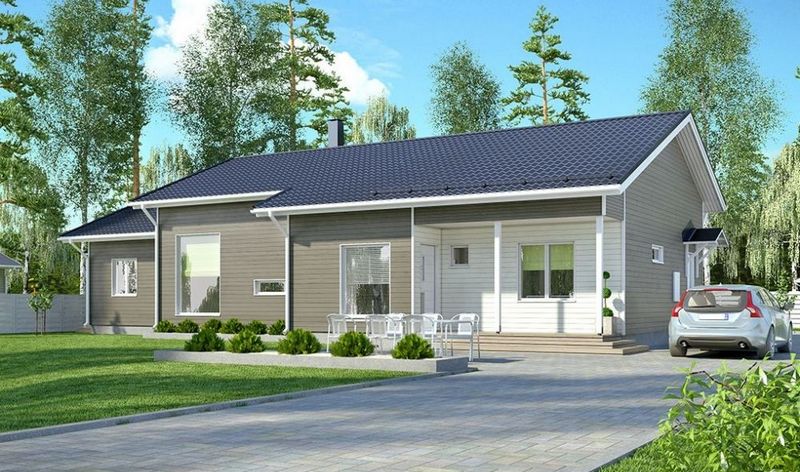
prefabricated house LLC "Pod klyuch" variant "Velya
Advantages:
- The price corresponds to the declared quadrature;
- The presence of a sauna;
- Possibility of living in any season.
Flaws:
2nd place: "LLC "Turnkey" option "Pinega"
The structure has a total living area of 183 m2 on a 2-storey space, there are 6 living rooms, the total dimensions are 16 x 9 m, there is an extension bay window that can be used as a garage for a small car or a simple storage room. Despite the presence of two floors of the main residential block, the structure itself does not look particularly large. Preferably used as a summer residence. The cost in the basic configuration is 4,700,000 rubles.
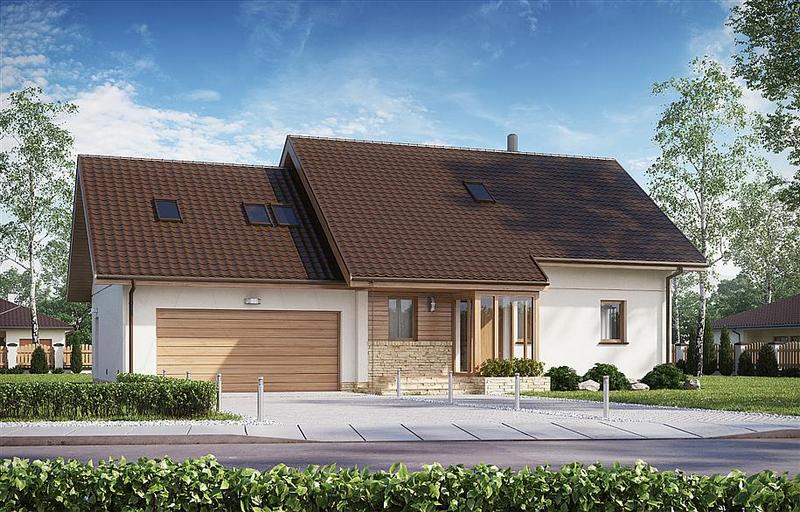
prefabricated house LLC "Pod klyuch" option "Pinega
Advantages:
- The presence of a bay window (garage, storage room);
- 2 residential floors;
- Large overall area.
Flaws:
1st place: "LLC "Turnkey" option "Aramant"
According to this project, the total area of the dwelling is 169 m2, there are only 4 living rooms, floors - 2, building dimensions - 11 x 10 m. The model is positioned as a full-fledged summer residence: a veranda and a balcony are provided. It is allowed to cover the panels with any decorative materials from wood to mosaic.The gable roof perfectly protects the interior from precipitation during the unused period (autumn, winter). The veranda can be equipped with individual sun loungers. The cost in the basic configuration is 5,070,000 rubles.
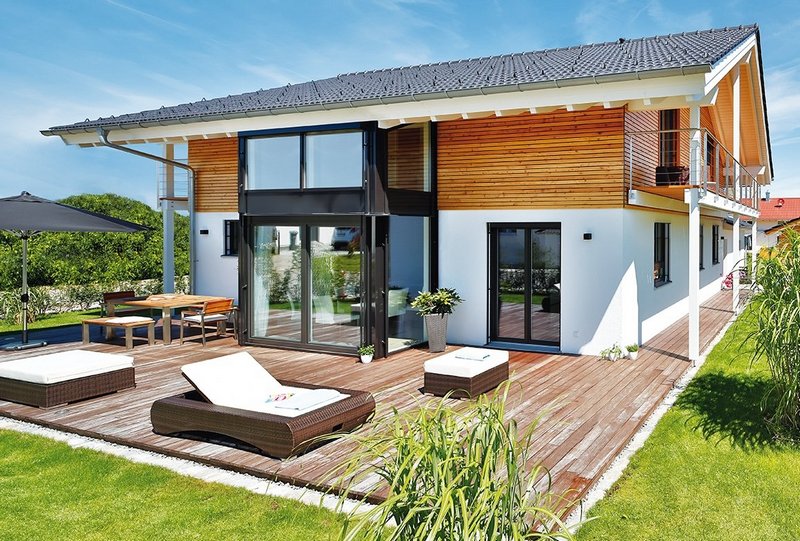
prefabricated house LLC "Pod klyuch" option "Aramant
Advantages:
- 2-storey building;
- Possibility of external cladding/finishing;
- Balcony and veranda available.
Flaws:
Conclusion
In cases where the budget and terms of building a dwelling are extremely tight, and you really want to have your own “corner”, then a prefabricated house will be the best solution. The idea to build such structures came from foreigners and is now gaining unprecedented popularity in the Russian Federation. Fast construction time and the global completion of all work is their most important advantage. As well as the price. Therefore, if the expectations of construction and the cost of a monolithic concrete or brick structure are insurmountable, then the accelerated technologies under consideration will easily overcome this.